
DiVYA
PHONE : +91-8374485833,
Mail : storagetanks@mail.com
INDUSTRIAL PIPING DESIGN CONULTANCY SERVICES

Compressor Piping System Design Services
Piping Design Consultants- Turbine Piping | Divya Engineering
Turbine piping refers to the network of pipes that deliver steam, water, or other fluids to and from turbines in power plants, particularly in thermal or nuclear power generation facilities. These piping systems are crucial for efficient operation, safety, and maintaining the mechanical integrity of the turbine units.
Key Aspects of Turbine Piping:
-
Steam and Condensate Systems:
-
Steam Supply Piping: This includes the pipes that deliver high-pressure steam from the boiler to the turbine. The pressure and temperature of the steam must be controlled to ensure the turbine operates within its specified range.
-
Condensate Return Piping: After steam exits the turbine, it condenses and is returned to the boiler as water, which is then reheated to generate more steam. Condensate piping must be well-insulated to prevent heat loss and to maintain efficiency.
-
-
Feedwater System:
-
This system brings treated water into the boiler after it has been condensed. It also includes piping to ensure the proper flow rates and pressure levels to prevent damage to the turbine.
-
-
Cooling Systems:
-
In many power plants, cooling systems are required to cool down the exhaust steam from the turbine. These systems involve additional piping to circulate cooling water or air, especially in plants using cooling towers.
-
-
Pressure and Flow Control:
-
Specialized valves, such as control valves, pressure relief valves, and check valves, are installed in turbine piping systems to regulate the flow of steam or water. These valves help maintain optimal pressure conditions and prevent dangerous surges that could damage the system.
-
-
Materials and Design:
-
Piping materials are selected based on factors such as temperature, pressure, and fluid type. Common materials include:
-
Carbon steel for lower-pressure systems.
-
Alloy steels and stainless steels for higher-pressure and high-temperature environments.
-
Copper-nickel alloys for certain cooling systems, especially for seawater applications.
-
-
The design also takes into account factors such as thermal expansion, vibrations, and potential corrosion.
-
-
Insulation:
-
Steam lines and condensate return pipes are usually insulated to reduce energy loss and improve thermal efficiency. Proper insulation also prevents accidental burns and helps maintain safe operating temperatures.
-
-
Safety Considerations:
-
Proper support and bracing of the piping are necessary to prevent undue stress and vibration from impacting the turbine or its components.
-
Piping must be designed with redundancy in mind, ensuring that if one pipe fails, the system can continue to operate.
-
-
Expansion Loops:
-
Due to the high temperatures and pressure variations, turbine piping must accommodate thermal expansion. Expansion loops or compensators are included to prevent pipes from bending or rupturing under these conditions.
-
-
Turbine Exhaust Systems:
-
After passing through the turbine blades, exhaust steam is often directed through a condenser. The piping from the turbine to the condenser is a key element in ensuring efficient energy recovery and cooling.
-
​
"Divya Engineering offers expert piping design consultancy services specializing in Trbine Piping systems. We provide innovative and cost-effective solutions tailored to your project needs
TURBINE PIPING DESIGN AND DRAFTING
Divya Engineering is a consultancy specializing in providing expert design services for turbine piping systems. Their offerings encompass a variety of services, including the creation of detailed CAD drawings, conducting design calculations, performing pipe stress analysis, and developing 3D models, along with fabrication and erection drawings. The team pays close attention to critical aspects such as material selection, support detail design, and project management, while ensuring compliance with key standards like ASME B31.1 and ASME B31.3. In addition to turbine systems, Divya Engineering also serves industries such as oil and gas, petrochemicals, and power generation, offering services like piping layout optimization, support design, stress analysis with CAESAR II, and the creation of Piping and Instrument Diagrams (P&IDs), among others.
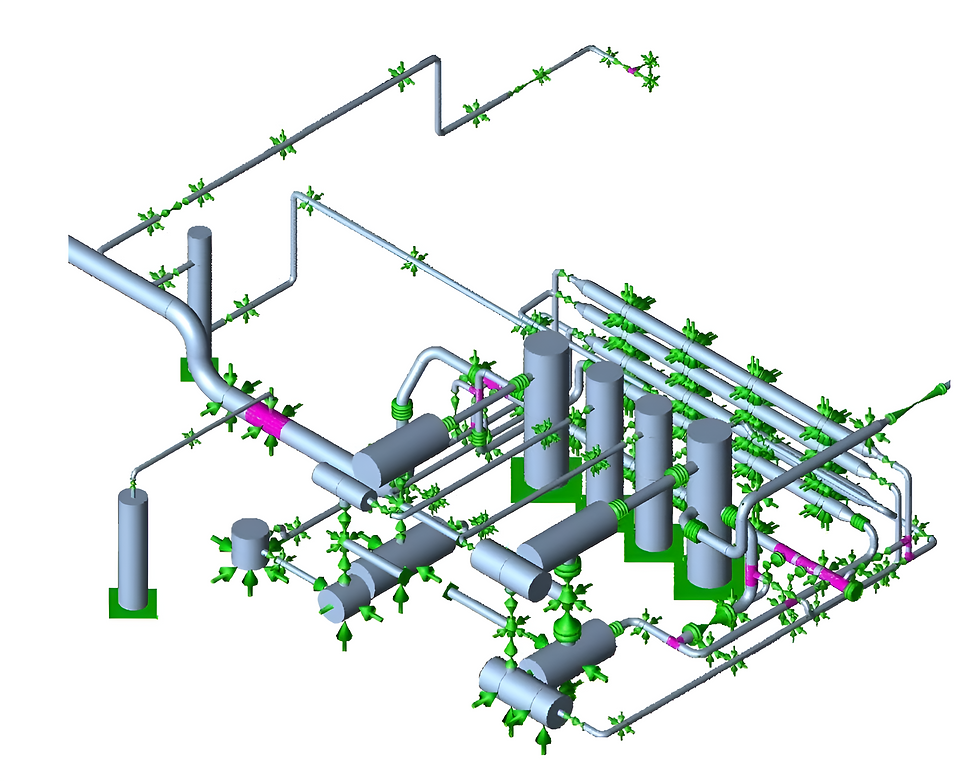
TURBINE PIPING LAYOUT AND ROUTING
Divya Engineering's Turbine Piping Design Services span a broad range of essential offerings, including Piping Layout and Routing. This process is essential for designing turbine distribution systems across residential, commercial, and industrial sectors. It ensures the safe and efficient transportation of fluids through the piping network, addressing space constraints, optimizing system performance, and facilitating maintenance. Tools Used for Piping Layout and Routing:
-
AutoCAD: Used for both 2D and 3D design, AutoCAD is commonly employed to create turbine piping layouts and routing plans.
-
Revit: This software is particularly effective for Building Information Modeling (BIM), especially in the context of turbine piping systems within structures.
Plant 3D: Tailored for industrial turbine systems, Plant 3D is used to model routing and optimize piping configurations

TURBINE PIPING SUPPORT DESIGN
A crucial part of Divya Engineering's Turbine Piping Design Services includes Piping Support Design. This aspect is vital for ensuring the structural integrity, operational efficiency, and safety of turbine distribution frameworks throughout the system's lifecycle. The service focuses on creating robust supports, hangers, and brackets that secure the pipes and protect them from damage caused by movement, vibration, thermal expansion, and other external factors. To accomplish this, advanced software tools such as CAESAR II for piping stress analysis and support design, AutoCAD Plant 3D for 3D modeling layout integration, and Revit for 3D visualization in integrated designs are utilized.

TURBINE PIPING MATERIAL SELECTION
Piping material selection is another critical area in turbine piping design. Divya Engineering assists clients in selecting the most appropriate materials for their turbine systems, ensuring the system's durability, efficiency, and ability to withstand varying pressures, temperatures, and other operating conditions. The material selection process takes into account factors such as pressure, temperature resistance, and cost efficiency, ensuring the chosen materials will contribute to the system's optimal performance and long-term sustainability

TURBINE PIPING STRESS ANALYSIS
Piping stress analysis is a key component of Divya Engineering's turbine piping design services. This analysis ensures that the system is structurally sound and able to withstand the stresses encountered throughout its lifecycle. In turbine systems, stress analysis is essential for identifying potential issues such as thermal expansion, pressure surges, vibrations, and mechanical loads, which could lead to failures, leaks, or system degradation. Industry Standards and Codes for Piping Stress Analysis: Divya Engineering adheres to industry standards when conducting piping stress analysis, including:
-
ASME B31.3: This standard addresses process piping systems, including the necessary design, materials, and considerations for turbine and industrial piping systems.
-
ASME B31.1: This code focuses on power piping, covering steam, turbine, and fluid systems.

TURBINE PIPING AND INSTRUMENTATION DIAGRAMS (P&IDS):
Divya Engineering’s Turbine Piping Design Services also include the creation of Piping and Instrumentation Diagrams (P&IDs). P&IDs are crucial tools in the design, operation, and maintenance of turbine piping systems. These diagrams are comprehensive graphical representations that detail the relationships between the system's components, such as pipes, equipment, valves, instruments, and control systems. They are vital for understanding fluid flow, highlighting key components like turbines, filters, tanks, and associated instrumentation. By integrating all these elements, P&IDs serve as a blueprint for the entire system, ensuring safe operation and simplifying future troubleshooting

TURBINE DEVELOPMENT OF PIPING SPECIFICATIONS AND STANDARDS
The development of piping specifications and standards is another cornerstone of Divya Engineering’s turbine piping design services. These specifications ensure that the turbine piping system is designed, installed, and maintained according to consistent, reliable, and efficient practices. This is particularly important in ensuring the safety, performance, and durability of the system, while ensuring compliance with both local and international regulations.
Divya Engineering adopts a structured, phased methodology when developing these specifications and standards, ensuring comprehensive coverage throughout the project lifecycle. This process is essential for turbine piping design, as it guarantees the correct selection of materials, accurate pipe sizing, and adherence to national and international standards. By providing detailed piping specifications, Divya Engineering ensures that turbine systems operate at peak efficiency
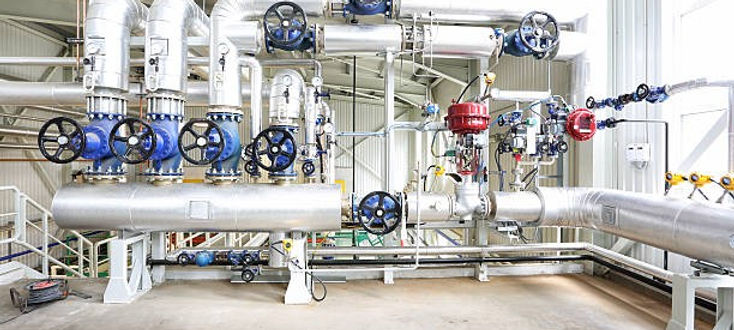
TURBINE PIPE SIZING AND HYDRAULIC CALCULATIONS
The turbine piping design process also involves key components such as pipe sizing and hydraulic calculations. These are critical for ensuring the efficiency, reliability, and longevity of the system. Proper pipe sizing and hydraulic analysis are essential for optimizing turbine system performance across various sectors, including industrial, commercial, and municipal applications. Divya Engineering employs a comprehensive and methodical approach to pipe sizing and hydraulic calculations, ensuring that each system component contributes to optimal performance, reduces operational costs, and enhances system longevity.
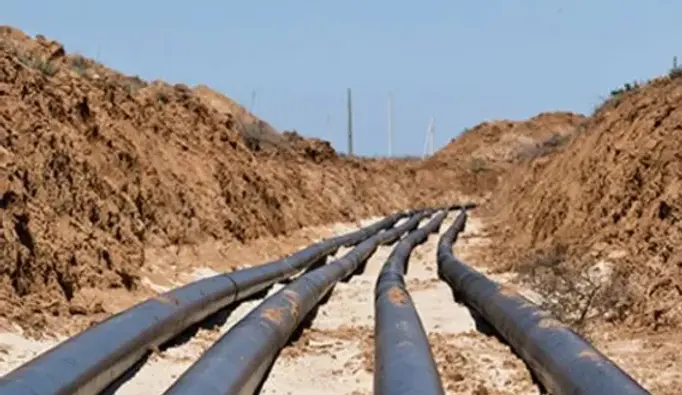
TURBINE 3D MODELING AND DESIGN
In modern turbine system design, 3D modeling plays an essential role in ensuring accurate and efficient representations of the piping systems. Divya Engineering provides advanced 3D modeling and design services to ensure that turbine piping systems are meticulously designed, optimized, and executed with precision, significantly reducing the risk of errors or rework. 3D design facilitates better visualization, simulation, and analysis of the entire system before construction, helping identify potential challenges early on and refining the design for real-world conditions.

TURBINE ISOMETRIC/FABRICATION/ERECTION DRAWINGS
Finally, the creation of isometric, fabrication, and erection drawings is crucial in the turbine piping design process. These drawings provide clear, detailed instructions for constructing and installing turbine systems. Isometric Drawings offer a 3D representation of the system, drawn at a 30-degree angle to convey the layout and orientation of pipes, valves, and other components. Fabrication Drawings detail the specifics of each piping component, including materials, dimensions, and assembly instructions, while Erection Drawings guide the installation team in positioning and assembling pipes and equipment on-site.
Through these detailed drawings, Divya Engineering ensures that every aspect of the turbine piping system is built accurately and efficiently, in compliance with all relevant codes and standards, thus providing a solid foundation for optimal system performance.
Turbine Piping Design Services
Piping Design Consultants- Turbine Piping | Divya Engineering
Piping Design and Drafting: Creating detailed CAD drawings and design calculations for Turbine piping systems used in power plants, refineries, and other industrial facilities.
​
Pipe Stress Analysis: Performing static and dynamic stress analysis using software like CAESAR II to ensure the Turbine piping system can withstand operational and environmental stresses.
​
3D Modeling and Design: Using software such as PDS, PDMS, or Auto Plant to create 3D models of Turbine piping systems for better visualization and accuracy.
​
Isometric/Fabrication/Erection Drawings: Preparing detailed drawings for the fabrication and installation of Turbine piping systems.
​
Support Detail Drawing Preparation: Designing and detailing the necessary supports for the Turbine piping system to ensure stability and safety.
​
Project Management: Managing the entire Turbine piping design project from initial conceptualization through fabrication and commissioning.
​
Compliance with Standards: Ensuring that the design complies with relevant standards such as ASME B31.1 for power piping and ASME B31.3 for process piping.
​
BILL OF MATERIAL, INSULATION & EXPANSION JOINTS
​
​
Designing turbine piping systems presents several challenges
due to the complex and high-stakes nature of the environments in which these systems operate. Here are some of the key challenges faced during turbine piping system design:
1. Thermal Expansion and Contraction:
Turbine piping systems often experience extreme temperature variations during operation. These temperature fluctuations can cause pipes to expand and contract, which needs to be accounted for in the design. Engineers must ensure that the system can handle this thermal movement without causing stress or damage to the components, joints, or supports.
2. Pressure and Flow Rate Variations:
Turbine piping systems are designed to transport fluids, such as steam or gas, at high pressures and flow rates. Variations in pressure or flow can lead to issues such as erosion, vibration, or cavitation. The design must include pressure relief mechanisms, appropriate pipe sizing, and control valves to manage these fluctuations effectively.
3. Vibration and Mechanical Stress:
The high-speed operation of turbines can generate significant vibrations, which can be transferred through the piping system. These vibrations can cause mechanical stress on the pipes, joints, and supporting structures. Proper vibration isolation and the design of flexible piping elements are necessary to prevent damage.
4. Corrosion and Erosion Resistance:
Turbine systems often deal with harsh conditions, including high temperatures and corrosive fluids (such as steam or chemicals). The piping materials used must be resistant to corrosion and erosion to ensure longevity and reliability. Selecting the right materials and coatings is a critical challenge in the design process.
5. Space Constraints and Layout Optimization:
Turbine piping systems are often located in congested areas, such as power plants or industrial facilities, where space is limited. Designing an efficient layout that minimizes space while ensuring safety, accessibility, and ease of maintenance is a complex task. The design must also allow for proper routing of pipes to avoid interference with other systems or structures.
6. System Integration:
Turbine piping systems do not operate in isolation. They must be seamlessly integrated with other mechanical and electrical systems, such as pumps, valves, and heat exchangers. Ensuring compatibility with existing systems while adhering to industry codes and standards is a constant challenge.
7. Safety Considerations:
Safety is paramount in the design of turbine piping systems. The design must account for emergency shutoff valves, pressure relief devices, and fail-safe mechanisms to protect the system from potential failures or hazardous situations. The system should be designed to prevent leaks, bursts, and other safety risks.
8. Compliance with Standards and Regulations:
Turbine piping systems must adhere to a variety of local and international standards, including ASME, ASTM, and API regulations. Meeting these regulatory requirements while also optimizing for cost-efficiency and performance can be challenging.
9. Maintenance and Accessibility:
Turbine piping systems must be designed with ease of maintenance in mind. This involves ensuring that components are accessible for inspection, cleaning, and replacement. The design should allow for the efficient removal and installation of parts, which can be particularly difficult in confined spaces.
10. Environmental Impact:
Sustainability is an important consideration in turbine piping system design. Engineers must focus on reducing environmental impacts, such as minimizing leaks or emissions, and consider energy efficiency throughout the system. The use of eco-friendly materials and processes is also becoming increasingly important in modern designs.
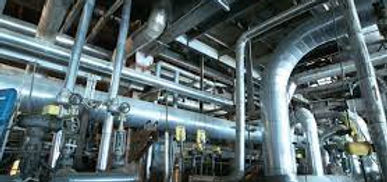

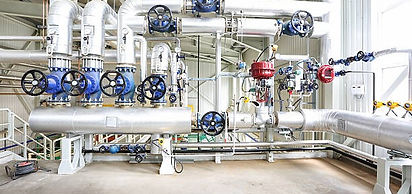
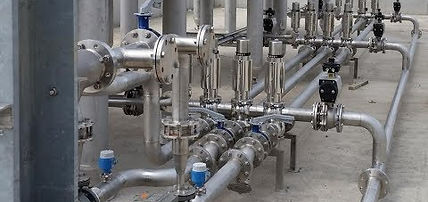