
DiVYA
PHONE : +91-8374485833,
Mail : storagetanks@mail.com
INDUSTRIAL PIPING DESIGN CONULTANCY SERVICES

Liquid Oxygen/ Nitrogen
Piping Design Services
Piping Design Consultants- Liquid Oxygen/ Nitrogen Piping | Divya Engineering
"Divya Engineering offers expert piping design consultancy services specializing in Liquid oxygen (LOX) and liquid nitrogen (LIN) Piping systems. We provide innovative and cost-effective solutions tailored to your project needs
Liquid oxygen (LOX) and liquid nitrogen (LIN) piping systems are critical components in various industrial applications, such as in hospitals, aerospace, and cryogenics. These systems are designed to handle gases at extremely low temperatures, often below -150°C (-238°F), which requires special materials and construction techniques to ensure safety and reliability.
Here are some key considerations when dealing with LOX and LIN piping systems:
1. Materials
-
Piping Materials: Pipes must be made from materials that can withstand very low temperatures without becoming brittle. Common materials used include:
-
Stainless Steel (316L, 304L): Preferred for LOX and LIN applications due to its resistance to low temperatures and corrosion. It retains good mechanical properties even at cryogenic temperatures.
-
Copper: In some cases, copper is used, especially for smaller pipes or when flexibility is needed. However, it's less common for LOX due to the potential for embrittlement.
-
Aluminum: For lower-pressure systems, aluminum alloys can be used, but its usage is limited due to thermal expansion properties.
-
-
Insulation: Due to the low temperatures, proper insulation is necessary to prevent heat ingress, which could lead to the vaporization of the cryogenic liquid. Common insulation materials include:
-
Vacuum Insulated Piping (VIP): Where the space between the outer and inner pipe is evacuated to reduce heat transfer.
-
Foam Insulation: Polyurethane or phenolic foam can be used, though not as effective as vacuum insulation.
-
-
Seal Materials: The sealing materials must be compatible with cryogenic conditions. Typically, elastomers or PTFE (polytetrafluoroethylene) are used, but they need to maintain their properties at extremely low temperatures.
2. Design Considerations
-
Pressure and Flow: The system must be designed to handle the pressure requirements of the specific LOX or LIN application. The pressure drop and flow rate need to be carefully calculated to ensure the system operates within safe and optimal parameters.
-
Thermal Expansion: Cryogenic fluids cause contraction in piping and components. The design must include expansion loops, bends, or flexible joints to accommodate this.
-
Ventilation: Any failure or blockage in the piping can cause the cryogenic liquid to evaporate, creating high-pressure gas. Venting systems must be in place to prevent excessive pressure build-up.
-
Valves and Fittings: These must be designed for low-temperature operation. Common types include cryogenic valves, which are often ball valves or globe valves that are specifically built to handle the unique conditions of LOX/LIN systems.
3. Safety Considerations
-
Material Compatibility: Oxygen is highly reactive, especially at low temperatures. Special care must be taken to ensure that all materials in contact with liquid oxygen are oxygen-compatible, meaning they won’t ignite or combust under cryogenic conditions.
-
Purge Systems: Oxygen and nitrogen systems should be purged of any contaminants or air (which could contain moisture or hydrocarbons) before cryogenic fluids are introduced. Purging systems using nitrogen are commonly employed.
-
Leak Detection: Since both LOX and LIN are colorless and odorless, detecting leaks is critical. Methods such as pressure sensors, temperature sensors, and occasionally gas detectors are used to identify leaks.
-
Personal Protective Equipment (PPE): Due to the risk of frostbite, explosion, and oxygen-enriched environments, workers need to wear appropriate PPE, including face shields, cryogenic gloves, and proper footwear.
4. Installation and Maintenance
-
Cryogenic Piping Layout: The piping layout must account for the system’s intended function. For example, in medical applications, the piping may need to be run throughout a hospital complex to supply oxygen to different areas. In aerospace, piping systems must be designed for extreme vibration and dynamic conditions.
-
Maintenance: Regular inspection and maintenance are essential, as cryogenic pipes can develop issues over time due to thermal cycling, pressure variations, and the potential for contaminants entering the system.
5. Applications
-
Aerospace: LOX and LIN are commonly used as propellants in rocket engines. In these systems, the design focuses on minimizing weight and maximizing safety under extreme conditions.
-
Medical and Industrial Gas Supply: Hospitals rely on liquid oxygen for patient breathing systems. Liquid nitrogen is also used for cooling equipment and cryogenic preservation. In industrial applications, these gases are used for freezing and cooling processes.
-
Cryogenics and Research: Many research institutions and laboratories use LOX and LIN in cooling superconducting magnets or conducting low-temperature experiments.
6. Flow and Pressure Calculations
-
For both LOX and LIN, the calculation of flow rates, pressure drops, and system capacity is critical. Factors such as pipe diameter, temperature, and fluid density play significant roles in the design process. Cryogenic fluids also have low densities, which means they require more careful consideration of the flow dynamics.
Conclusion
Designing and installing piping systems for LOX and LIN involves addressing unique challenges such as extreme temperatures, material selection, insulation, and safety. It requires specialized knowledge of cryogenics, fluid dynamics, and materials engineering. A well-designed system will prioritize safety, efficiency, and reliability, ensuring that liquid oxygen or nitrogen can be safely transported and used for a variety of applications.
Piping Design and Drafting: Creating detailed CAD drawings and design calculations for Liquid Oxygen/ Nitrogen piping systems used in power plants, refineries, and other industrial facilities.
​
Pipe Stress Analysis: Performing static and dynamic stress analysis using software like CAESAR II to ensure the Liquid Oxygen/ Nitrogen piping system can withstand operational and environmental stresses.
​
3D Modeling and Design: Using software such as PDS, PDMS, or Auto Plant to create 3D models of Liquid Oxygen/ Nitrogen piping systems for better visualization and accuracy.
​
Isometric/Fabrication/Erection Drawings: Preparing detailed drawings for the fabrication and installation of Liquid Oxygen/ Nitrogen piping systems.
​
Support Detail Drawing Preparation: Designing and detailing the necessary supports for the Liquid Oxygen/ Nitrogen piping system to ensure stability and safety.
​
Project Management: Managing the entire Liquid Oxygen/ Nitrogen piping design project from initial conceptualization through fabrication and commissioning.
​
Compliance with Standards: Ensuring that the design complies with relevant standards such as ASME B31.1 for power piping and ASME B31.3 for process piping.
​
BILL OF MATERIAL, INSULATION & EXPANSION JOINTS
​
​
Challenges Liquid oxygen/ Nitrogen Piping design
​
Designing piping systems for Liquid Oxygen (LOX) and Liquid Nitrogen (LIN) presents several significant challenges due to the extreme properties of these cryogenic gases. Both gases must be stored and transported at temperatures well below freezing, with Liquid Oxygen being stored at around -183°C (-297°F) and Liquid Nitrogen at -196°C (-320°F). The extreme cold, combined with the gases' flammability (in the case of oxygen), presents unique design considerations. Below are the primary challenges in designing LOX and LIN piping systems:
1. Cryogenic Temperatures:
Both LOX and LIN must be transported and stored at cryogenic temperatures, which poses several risks to materials and system performance. At these temperatures, most materials become brittle and lose their strength, which can lead to failure or cracking in piping systems.
-
Material selection is critical to ensure that the pipes, valves, seals, and fittings can handle the extreme low temperatures without becoming brittle or prone to cracking. Commonly used materials include stainless steel, aluminum alloys, and nickel alloys, which are specially designed for cryogenic applications.
-
Special attention must be given to thermal expansion and contraction as materials shrink and expand with temperature changes. These fluctuations must be accounted for to prevent mechanical stress or failure in the piping system.
2. Thermal Insulation:
Preventing heat gain is crucial to maintaining the cryogenic state of LOX and LIN. Heat transfer can lead to the boil-off of liquid gas, reducing efficiency and causing safety concerns.
-
The system must be properly insulated to prevent heat from reaching the liquid and turning it into gas (boil-off gas). This requires high-performance insulation materials, such as vacuum-insulated panels or foam-based materials, which are highly resistant to thermal conductivity.
-
Designing the insulation for long-term durability and resistance to environmental factors like humidity, water ingress, and mechanical wear is a challenge. This is particularly important for outdoor installations or systems in harsh environments.
3. Material Brittle Fracture and Compatibility:
Cryogenic temperatures increase the risk of brittle fracture in metals and other materials. Piping systems must be constructed from materials that can withstand the extreme cold without becoming brittle or prone to cracking.
-
Materials like stainless steel (304L or 316L), aluminum alloys, and specially engineered alloys are selected for their cryogenic compatibility. Materials need to be carefully chosen based on their low-temperature toughness, fatigue resistance, and ductility.
-
Stress-corrosion cracking (SCC) and hydrogen embrittlement are also potential risks, particularly when the system is exposed to both high pressures and low temperatures, requiring materials that can resist these phenomena.
4. Pressure Control:
Liquid oxygen and liquid nitrogen are typically transported under high pressures to maintain their liquid state. However, the pressure needs to be controlled and regulated to avoid over-pressurization, which can cause piping rupture or failure.
-
Pressure regulators, valves, and safety relief devices must be carefully designed and chosen to handle the high pressures associated with LOX and LIN systems.
-
The system must include pressure relief valves (PRVs) to release pressure in case of over-pressurization. High-pressure piping is often necessary, which means that the walls of the piping must be thick enough to withstand the internal pressure, but also flexible enough to allow for thermal expansion and contraction.
5. Flammability of Liquid Oxygen:
Liquid oxygen is highly reactive and flammable, particularly when it comes into contact with combustible materials or oil. Even small leaks in the system can pose catastrophic safety risks, such as fire or explosions.
-
Systems transporting LOX require strict attention to cleanliness to avoid contamination by oils, greases, or any material that could ignite in the presence of oxygen. This includes ensuring that all components of the piping system, including valves and fittings, are free from hydrocarbons.
-
Additionally, oxygen-enriched environments increase the risk of combustion. Therefore, piping systems must be designed to avoid any sources of ignition and must be constructed with non-combustible materials. Explosion-proof fittings and spark-proof tools are often needed during installation and maintenance.
6. Leak Detection and Prevention:
Detecting leaks in cryogenic systems is critical, as even small leaks can be hazardous, particularly in systems handling liquid oxygen. Oxygen leaks are a serious concern due to the risk of ignition in oxygen-enriched environments.
-
Leak detection technology, such as infrared sensors or hydrogen leak detectors, must be incorporated into the system to detect any loss of liquid oxygen or nitrogen quickly. This requires sophisticated sensors designed to function in cryogenic conditions.
-
Seals and joints in cryogenic systems must be extremely durable and resistant to low-temperature brittleness, mechanical stresses, and vibration. Leaks at these points can compromise the integrity of the system and must be avoided.
7. Vibration and Mechanical Stress:
Cryogenic piping systems are often subject to vibrations due to pumps, compressors, and other equipment. Over time, these vibrations can lead to fatigue failures in piping materials, particularly at joints, welds, and fittings.
-
Proper pipe supports, expansion joints, and vibration dampeners must be integrated into the system design to reduce mechanical stress and prevent damage.
-
Designers must also ensure that piping systems are flexible enough to accommodate thermal expansion and contraction without causing stress on the system.
8. Environmental Considerations:
LNG, LOX, and LIN systems are often installed in outdoor or exposed environments, which means that they are subject to environmental conditions such as wind, rain, snow, seismic activity, and extreme temperatures.
-
Systems must be designed to withstand the environmental conditions of the installation location, including protection against corrosion from exposure to saltwater (in coastal areas) or chemicals in industrial areas.
-
Insulation materials must also be chosen for their resistance to environmental factors such as moisture and UV degradation.
9. Regulatory Compliance and Safety Standards:
Due to the safety risks involved in handling and transporting cryogenic gases, LOX and LIN piping systems must comply with stringent regulatory standards. These standards are set by bodies such as the American Society of Mechanical Engineers (ASME), the National Fire Protection Association (NFPA), and the Occupational Safety and Health Administration (OSHA).
-
Designers must ensure that systems meet all applicable codes for pressure vessels, piping, and safety equipment. Compliance with local and international standards is essential to ensure safety and avoid penalties.
-
Regular inspections and certifications are required throughout the system’s lifecycle to ensure that the piping system continues to operate safely and efficiently.
10. Cost Management:
While safety and performance are the top priorities, managing the costs associated with designing and building cryogenic systems is a challenge. Materials suitable for cryogenic temperatures, as well as insulation and specialized equipment, can be expensive.
-
Designers must balance the cost of materials with the need for safety and performance. Efficient design and material sourcing, as well as optimizing system configuration, can help reduce overall costs without compromising safety.
Conclusion: Designing Liquid Oxygen (LOX) and Liquid Nitrogen (LIN) piping systems requires specialized knowledge and expertise to address the unique challenges presented by cryogenic temperatures, pressure management, flammability, and material compatibility. Proper design ensures the safe, efficient, and reliable transportation of these gases while maintaining compliance with industry safety standards. By selecting the right materials, ensuring thermal and mechanical stability, and incorporating state-of-the-art safety systems, these challenges can be successfully mitigated to create effective and long-lasting cryogenic piping solutions.
Get smarter responses, upload files and images, and more.
Log in
Sign up
ChatGPT can make mistakes. Check important info.


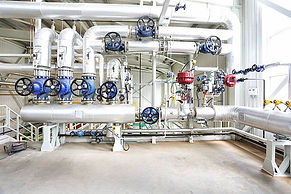
