
DiVYA
PHONE : +91-8374485833,
Mail : storagetanks@mail.com
INDUSTRIAL PIPING DESIGN CONULTANCY SERVICES

Naphtha Piping System Design Services
Piping Design Consultants- Naphtha Piping | Divya Engineering
"Divya Engineering offers expert piping design consultancy services specializing in Naphtha Piping systems. We provide innovative and cost-effective solutions tailored to your project needs
A naphtha piping system refers to the infrastructure used to transport naphtha (a flammable hydrocarbon mixture) through pipelines. Naphtha is often used as a feedstock in the production of gasoline, chemicals, and petrochemicals. These piping systems are typically part of large industrial facilities such as refineries, chemical plants, and petrochemical complexes.
Key Elements of a Naphtha Piping System:
-
Materials:
-
The piping used in naphtha systems must be resistant to corrosion, as naphtha can be aggressive on materials like steel. Common materials include carbon steel, stainless steel, and sometimes plastic-lined piping for additional corrosion protection.
-
-
Design and Safety:
-
Naphtha is highly flammable and volatile, so special care is taken in the design of the piping system. This includes:
-
Leak detection systems to monitor for spills or leaks.
-
Pressure relief valves to prevent over-pressurization.
-
Flame arresters to prevent the risk of combustion in case of a leak.
-
Explosion-proof electrical components for areas where electrical systems are in proximity to the piping.
-
-
-
Pumps and Compressors:
-
Pumps are used to move naphtha through the system. These pumps must be designed for handling flammable liquids and can vary in type, such as centrifugal or positive displacement pumps.
-
Compressors are sometimes used, especially if the naphtha needs to be transported over long distances or if it's in a vaporized state.
-
-
Flow Control:
-
A system for controlling the flow rate, including control valves and flow meters, ensures that naphtha is being transported efficiently and safely through the pipeline. These components allow for remote or manual control of the pipeline system.
-
-
Pressure and Temperature Control:
-
Because naphtha is sensitive to changes in temperature and pressure, the system must be designed to maintain specific operational conditions. This could involve the use of insulated piping or heating systems to maintain proper flow, especially in colder environments.
-
-
Storage and Distribution:
-
Naphtha is often stored in tanks at various points along the pipeline, especially in refineries and distribution centers. The piping system is then connected to storage tanks, and the naphtha is transferred to these tanks or to distribution points for further processing.
-
-
Maintenance and Inspection:
-
Regular inspection and maintenance are crucial for ensuring the integrity of the piping system. This includes cleaning, pressure testing, and checking for any signs of leaks or deterioration in the pipes or fittings.
-
Applications:
-
Refineries: Naphtha is a crucial component in the refining process, and its transport between various units is done via the piping system.
-
Petrochemical Plants: It serves as a feedstock for the production of chemicals like ethylene and propylene.
-
Fuel Distribution: In some cases, naphtha is directly used in gasoline blending or as a fuel source, so pipelines are essential in moving it from refineries to distribution points.
​
NAPHTHA PIPING DESIGN AND DRAFTING
Naphtha Piping Design Services
Divya Engineering is a leading consultancy specializing in the design and optimization of Naphtha piping systems. With a focus on industries where the reliability and integrity of fuel transportation systems are critical, such as oil and gas, petrochemicals, power generation, and industrial applications, Divya Engineering provides a comprehensive range of services. These include the creation of detailed CAD drawings, pipe stress analysis, 3D modeling, and the development of fabrication/erection drawings. The company is committed to ensuring that every design maximizes both performance and safety, adhering to stringent industry standards such as ASME B31.1 and ASME B31.3. In addition to their core offerings, Divya Engineering is recognized for its innovative solutions in piping layout optimization, stress analysis with CAESAR II, and the creation of Piping and Instrumentation Diagrams (P&IDs) for diverse industries.
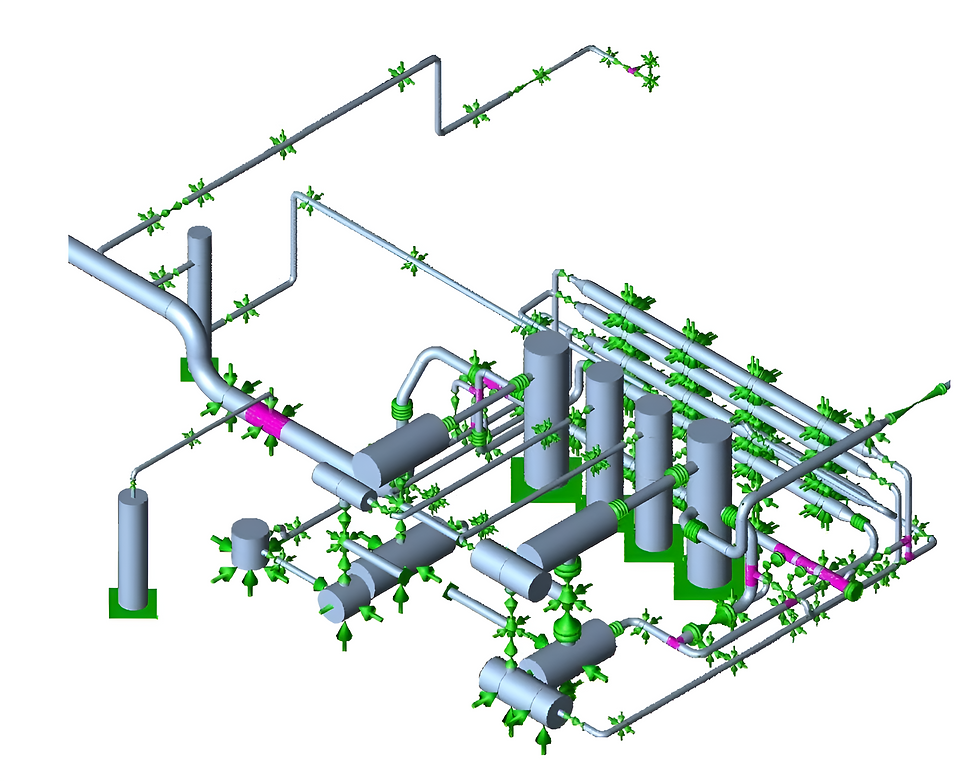
NAPHTHA PIPING LAYOUT AND ROUTING
Naphtha Piping Design and Engineering Expertise
Divya Engineering’s approach to designing Naphtha systems encompasses a wide array of specialized services necessary to build safe, efficient, and reliable fuel transportation systems. One of the most important stages in design is the Piping Layout and Routing phase. This ensures that Naphtha systems are engineered to meet both operational performance and stringent safety requirements. Effective layout planning is essential, particularly for industrial and energy sectors, to ensure the safe and efficient transportation of Naphtha, optimize system design, and facilitate ease of maintenance.
To achieve optimal outcomes, Divya Engineering employs cutting-edge tools that model, visualize, and meticulously plan piping systems for precision

NAPHTHA PIPING SUPPORT DESIGN
A key component of Naphtha piping design is Piping Support Design. This focuses on ensuring the structural stability of systems exposed to extreme temperatures, mechanical stresses, vibrations, and potentially corrosive conditions. Divya Engineering's expertise lies in creating durable supports, hangers, and brackets that ensure piping systems are secured correctly, minimizing the risks of failure. By utilizing advanced stress analysis tools like CAESAR II and AutoCAD Plant 3D, as well as BIM technologies like Revit, the company ensures that Naphtha piping systems are robust and resilient.

NAPHTHA PIPING MATERIAL SELECTION
Material Selection for Naphtha Systems
In Naphtha system design, selecting the right materials is essential for ensuring long-term performance. Divya Engineering works closely with clients to choose materials that are highly durable, resistant to the specific challenges posed by Naphtha, and capable of withstanding extreme operating conditions. Key factors like pressure tolerance, temperature resistance, and corrosion resistance are thoroughly evaluated to ensure system longevity and operational efficiency

NAPHTHA PIPING STRESS ANALYSIS
Piping Stress Analysis and Compliance
Piping Stress Analysis is critical for systems designed to transport Naphtha, as they must be able to endure pressure surges, thermal expansion, and external loads. Divya Engineering performs comprehensive stress evaluations to ensure that Naphtha piping systems are durable and safe, using top-tier software such as CAESAR II to simulate and analyze the stresses on piping. Ensuring compliance with industry standards is a top priority, with Divya Engineering strictly adhering to:
• ASME B31.3: Governs the design of process piping systems, ensuring systems can handle corrosive fluids like Naphtha effectively.
• ASME B31.1: Applies to power piping systems, including those used to transport high-temperature, high-pressure fluids such as Naphtha.
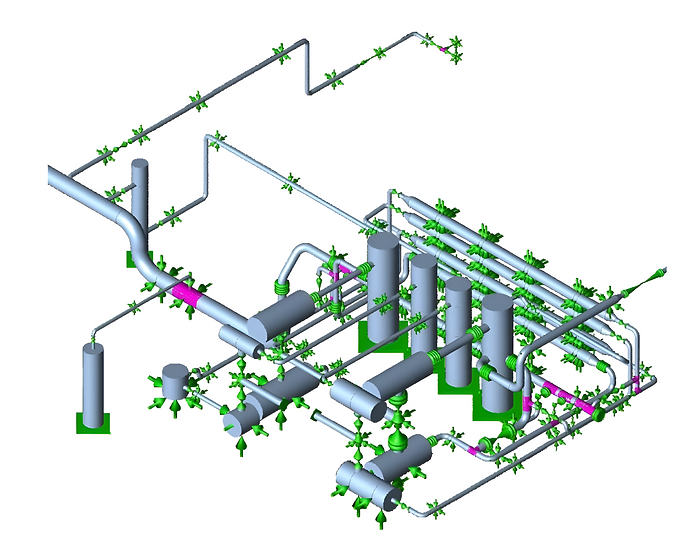
NAPHTHA PIPING AND INSTRUMENTATION DIAGRAMS (P&IDS):
P&IDs and Specification Development
Divya Engineering offers comprehensive services by creating Piping and Instrumentation Diagrams (P&IDs) for Naphtha systems. These diagrams illustrate the layout and components of the piping system, including valves, pumps, instrumentation, and control systems. P&IDs play a vital role in simplifying system troubleshooting and maintenance while ensuring safe system operation. Alongside P&IDs, Divya Engineering develops precise piping specifications and standards that define the necessary parameters for the installation, operation, and maintenance of Naphtha systems, ensuring compliance with both local and international standards for reliability and safety
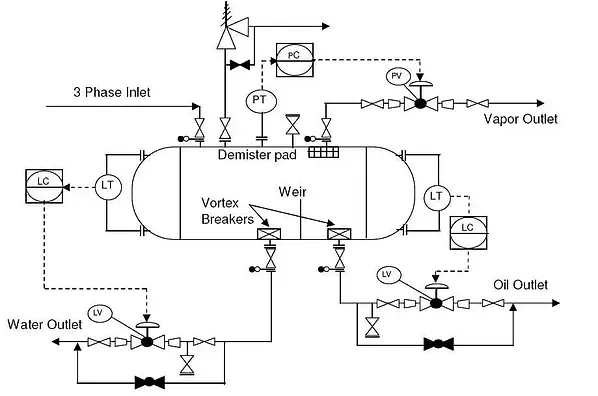
NAPHTHA DEVELOPMENT OF PIPING SPECIFICATIONS AND STANDARDS
The development of piping specifications and standards is another cornerstone of Divya Engineering’s turbine piping design services. These specifications ensure that the turbine piping system is designed, installed, and maintained according to consistent, reliable, and efficient practices. This is particularly important in ensuring the safety, performance, and durability of the system, while ensuring compliance with both local and international regulations.
Divya Engineering adopts a structured, phased methodology when developing these specifications and standards, ensuring comprehensive coverage throughout the project lifecycle. This process is essential for turbine piping design, as it guarantees the correct selection of materials, accurate pipe sizing, and adherence to national and international standards. By providing detailed piping specifications, Divya Engineering ensures that turbine systems operate at peak efficiency

NAPHTHA PIPE SIZING AND HYDRAULIC CALCULATIONS
Advanced Modeling and Hydraulic Calculations
To enhance the efficiency and cost-effectiveness of Naphtha systems, Divya Engineering uses hydraulic calculations and advanced pipe-sizing techniques. These methods ensure that the system operates at peak performance while minimizing operational costs. Through the use of 3D modeling technology, Divya Engineering provides highly accurate visual representations of the piping system, aiding in better planning, reducing errors, and ensuring more reliable construction outcomes. This 3D approach minimizes rework risks and facilitates a smoother transition from design to construction
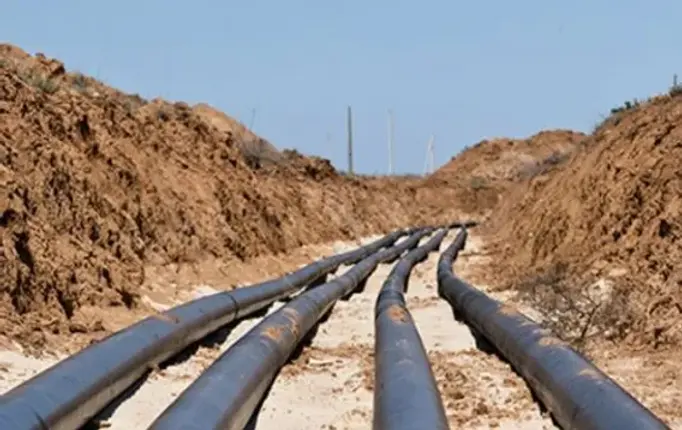
NAPHTHA 3D MODELING AND DESIGN
Through the use of 3D modeling technology, Divya Engineering provides highly accurate visual representations of the piping system, aiding in better planning, reducing errors, and ensuring more reliable construction outcomes. This 3D approach minimizes rework risks and facilitates a smoother transition from design to construction.

NAPHTHA) ISOMETRIC/FABRICATION/ERECTION DRAWINGS
Isometric, Fabrication, and Erection Drawings
Upon completion of the design phase, Divya Engineering generates a comprehensive set of Isometric Drawings, Fabrication Drawings, and Erection Drawings. These drawings are crucial for the precise construction and installation of Naphtha systems, ensuring that each component is fabricated, assembled, and installed according to specifications. Isometric drawings provide a 3D perspective of the entire system, while fabrication drawings detail individual components and materials. Erection drawings guide the on-site assembly process, ensuring that the final installation is aligned with the original design.
By offering these all-encompassing services, Divya Engineering ensures the successful design, implementation, and operation of Naphtha piping systems that are safe, reliable, and efficient in demanding industrial environments. Their commitment to quality, innovation, and compliance guarantees that every fuel transportation system meets the highest standards.
This revised version replaces "Diesel (HSD)" with "Naphtha" and provides a broader overview of Divya Engineering’s services in the context of Naphtha piping systems.
Naphtha Piping Design Services
Piping Design Consultants- Naphtha Piping | Divya Engineering
Piping Design and Drafting: Creating detailed CAD drawings and design calculations for Naphtha piping systems used in power plants, refineries, and other industrial facilities.
​
Pipe Stress Analysis: Performing static and dynamic stress analysis using software like CAESAR II to ensure the Naphtha piping system can withstand operational and environmental stresses.
​
3D Modeling and Design: Using software such as PDS, PDMS, or Auto Plant to create 3D models of Naphtha piping systems for better visualization and accuracy.
​
Isometric/Fabrication/Erection Drawings: Preparing detailed drawings for the fabrication and installation of Naphtha piping systems.
​
Support Detail Drawing Preparation: Designing and detailing the necessary supports for the Naphtha piping system to ensure stability and safety.
​
Project Management: Managing the entire Naphtha piping design project from initial conceptualization through fabrication and commissioning.
​
Compliance with Standards: Ensuring that the design complies with relevant standards such as ASME B31.1 for power piping and ASME B31.3 for process piping.
​
BILL OF MATERIAL, INSULATION & EXPANSION JOINTS
​
​
Challenges Naphtha Piping System design
​
Designing Naphtha Piping Systems comes with a series of unique and complex challenges due to the chemical properties of naphtha and the specific requirements of industrial operations. These challenges need to be carefully addressed to ensure that the system operates efficiently, safely, and in compliance with regulatory standards. Below are the key challenges faced during the design of Naphtha Piping Systems:
1. Material Selection and Corrosion Resistance:
Naphtha is a highly volatile and flammable substance, which requires the use of materials that can withstand its chemical properties without degrading over time. The piping system must be resistant to corrosion, particularly as naphtha may contain impurities or be transported at high temperatures. Choosing the right materials, such as stainless steel or coated carbon steel, is critical to ensure long-term durability and reliability.
2. Leak Prevention and Detection:
Naphtha is highly flammable and hazardous, making leak prevention a critical design consideration. Even small leaks can lead to catastrophic consequences, including fire, explosions, or environmental contamination. The system must be designed with leak-proof joints, seals, and fittings. Additionally, advanced leak detection technologies, such as sensors and monitoring systems, should be integrated to provide early warning and prevent accidents.
3. Thermal Expansion and Contraction:
Naphtha pipelines are often subjected to temperature fluctuations, which can cause the pipes to expand and contract. These thermal changes can lead to stress on the piping system, resulting in leaks or system failure. To address this, designers must incorporate expansion joints, flexible connectors, and proper supports to accommodate thermal movements and prevent damage to the piping.
4. Pressure and Flow Control:
Maintaining the correct pressure and flow rate within the piping system is vital for ensuring smooth and efficient operations. Naphtha needs to be transported at a controlled pressure to prevent vaporization or excessive pressure buildup, which could cause pipe ruptures. The system must be designed with the right specifications for pumps, pressure regulators, and valves to ensure that the naphtha flows consistently and safely under varying operational conditions.
5. Vapor and Fire Hazard Mitigation:
Due to naphtha's volatile nature, vaporization can occur during transportation, leading to fire and explosion risks. The piping system needs to be designed to manage these risks effectively by incorporating vapor recovery systems, adequate ventilation, and fire-resistant materials. Additionally, grounding and bonding of all equipment are necessary to prevent static electricity buildup, which could lead to sparks and ignition.
6. Environmental Impact and Spill Containment:
Naphtha is harmful to both the environment and public health if spilled or leaked. Designers must implement secondary containment systems, such as double-walled pipes or leak-proof barriers, to contain any accidental spills. Proper drainage systems and spill detection methods should also be included to prevent contamination of soil, water, or surrounding areas. Environmental regulations must be strictly followed to minimize the risk of pollution.
7. Compatibility with Other System Components:
Naphtha piping systems are typically part of a larger infrastructure that includes storage tanks, pumps, filtration systems, and heat exchangers. Integrating the piping system with other components can present challenges, particularly when considering the compatibility of materials and the coordination of system controls. Designers must ensure that the piping system integrates seamlessly with other equipment and maintains compatibility with the fluids or chemicals it interacts with.
8. Vibration and Mechanical Stress:
The pumps and equipment used in naphtha transportation can generate vibrations, which may lead to mechanical stress and fatigue on the piping system. Over time, these vibrations can weaken joints, fittings, and valves. The piping design must account for this potential by incorporating vibration dampening systems, such as flexible joints, mounts, and brackets, to reduce the impact of mechanical stress.
9. Compliance with Industry Standards and Regulations:
Naphtha piping systems must adhere to stringent industry standards and regulations set by organizations such as API (American Petroleum Institute), ASTM (American Society for Testing and Materials), NFPA (National Fire Protection Association), and local environmental authorities. Compliance with these regulations ensures that the system meets safety, performance, and environmental standards. Navigating these regulations and ensuring full compliance is a key challenge in the design process.
10. Maintenance and Inspection Access:
Ensuring that the piping system is accessible for regular maintenance and inspection is another design challenge. Routine inspections and preventive maintenance are essential to identify potential issues before they result in system failure. Designers must plan the layout to allow easy access to critical components for maintenance, such as valves, pumps, and pressure relief systems, without causing disruptions to ongoing operations.
11. Cost Management:
The design of naphtha piping systems often involves high-quality materials and advanced safety features, which can lead to significant project costs. Balancing the need for safety, durability, and performance with budget constraints is a common challenge. It’s essential to choose cost-effective materials, optimize system design, and plan for long-term operational costs to ensure both economic feasibility and safety.
12. Aging Infrastructure:
For many facilities, naphtha piping systems are part of an older infrastructure that may need upgrading or replacing. Upgrading or retrofitting existing systems can present challenges in ensuring compatibility with new technologies or materials. It also involves addressing issues such as corrosion, wear, and the potential for leaks in older systems.
Designing Naphtha Piping Systems requires a deep understanding of material science, fluid dynamics, safety protocols, and environmental impact mitigation. Overcoming these challenges ensures that the system operates efficiently, safely, and in compliance with all relevant regulations, minimizing risks while maximizing the performance of the entire fuel handling process.
Get smarter responses, upload files and images, and more.
Log in
Sign up


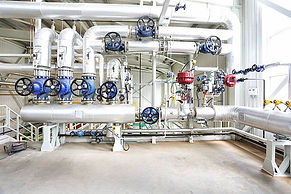
