
DiVYA
PHONE : +91-8374485833,
Mail : storagetanks@mail.com
INDUSTRIAL PIPING DESIGN CONULTANCY SERVICES

LPG Piping Design Services
Piping Design Consultants- LPG Piping | Divya Engineering
"Divya Engineering offers expert piping design consultancy services specializing in LPG Piping systems. We provide innovative and cost-effective solutions tailored to your project needs
LPG (Liquefied Petroleum Gas) piping systems are essential for the safe and efficient transportation of LPG from storage tanks to various appliances such as stoves, heaters, and industrial equipment. These systems need to be designed and installed to meet safety standards due to the highly flammable nature of LPG. Here's an overview of what LPG piping systems involve:
1. Components of an LPG Piping System
-
LPG Storage Tank: This is the primary source of LPG, often located outside the building. It’s typically a large pressurized cylinder or tank.
-
Piping: Piping systems are typically made from materials resistant to corrosion and capable of withstanding the pressure associated with LPG. The most common materials are:
-
Copper: Often used for domestic applications due to its corrosion resistance and ease of installation.
-
Steel: Used for larger industrial systems.
-
Aluminum: Lightweight and resistant to corrosion, sometimes used in residential setups.
-
Polyethylene (PE): Used for underground or external piping.
-
-
Valves: These control the flow of gas and include regulators, shut-off valves, and safety valves.
-
Fittings: Connect different sections of piping and include elbows, tees, unions, etc.
-
Regulators: These ensure that the gas is delivered at the proper pressure.
-
Meters: These measure gas consumption for billing purposes, particularly in commercial and industrial setups.
2. Design Considerations
-
Pipe Size: Proper sizing of the piping is crucial to ensure adequate gas flow. If the pipe is too small, it could result in inadequate supply to appliances, while a pipe that's too large may lead to unnecessary cost.
-
Pressure Drop: LPG systems should be designed to minimize pressure drop. A significant pressure drop can affect the performance of appliances.
-
Distance: The longer the distance between the LPG storage tank and the appliances, the greater the pipe diameter needs to be to compensate for pressure loss.
-
Ventilation: Adequate ventilation is essential, particularly in closed areas, to prevent gas buildup in case of leakage.
3. Safety Features
-
Leak Detection: Gas leaks are one of the most critical risks associated with LPG. Leak detection systems, such as gas detectors and alarms, should be installed.
-
Shut-off Valves: These should be strategically placed to allow the quick isolation of the LPG supply in case of an emergency.
-
Pressure Relief Valve: Protects the system from overpressure and potential bursts.
-
Proper Grounding: Pipes should be properly grounded to prevent static discharge, which could potentially ignite the gas.
-
Fire-resistant Insulation: LPG pipes may be insulated to prevent freezing or to protect them from high temperatures.
4. Installation Guidelines
-
External vs. Internal Piping: External piping is typically run along the outside of buildings and should be adequately protected from weather. Internal piping should be installed according to building codes and should be inspected regularly.
-
Clearances: Pipes should be routed with adequate clearance from other utilities, electrical systems, and combustible materials.
-
Testing: After installation, the system must be pressure-tested to ensure there are no leaks and the pressure is maintained.
6. Regulations and Standards
-
LPG systems need to comply with local and international standards for safety, such as:
-
NFPA 58 (National Fire Protection Association) - for safe storage and handling of LPG.
-
ASME B31.3 - for the design and construction of piping systems.
-
EN 1775 (European Standard) - for the design, installation, and maintenance of LPG systems in Europe.
-
7. Common Applications
-
Residential: Cooking, heating, and hot water supply.
-
Commercial: Restaurants, hotels, and laundromats often use LPG for cooking or heating.
-
Industrial: LPG is used in industrial processes, heating, or as a backup energy source in case of electrical failures.
LPG HYDROGEN PIPING DESIGN AND DRAFTING
LPG Piping Design Services
Divya Engineering is a leading consultancy renowned for its expertise in the design and optimization of LPG piping systems. With a primary focus on industries where safety, reliability, and efficiency in transportation systems are paramount—such as LPG production, storage, power generation, and industrial applications—Divya Engineering offers a comprehensive range of services. These services include detailed CAD drawings, pipe stress analysis, 3D modeling, and the creation of fabrication and erection drawings. The company is committed to ensuring that each design maximizes performance, safety, and operational excellence, in full compliance with stringent industry standards such as ASME B31.1 and ASME B31.3. Divya Engineering is also known for its innovative approach to piping layout optimization, stress analysis using advanced software like CAESAR II, and the development of Piping and Instrumentation Diagrams (P&IDs) for a broad array of industrial sectors.
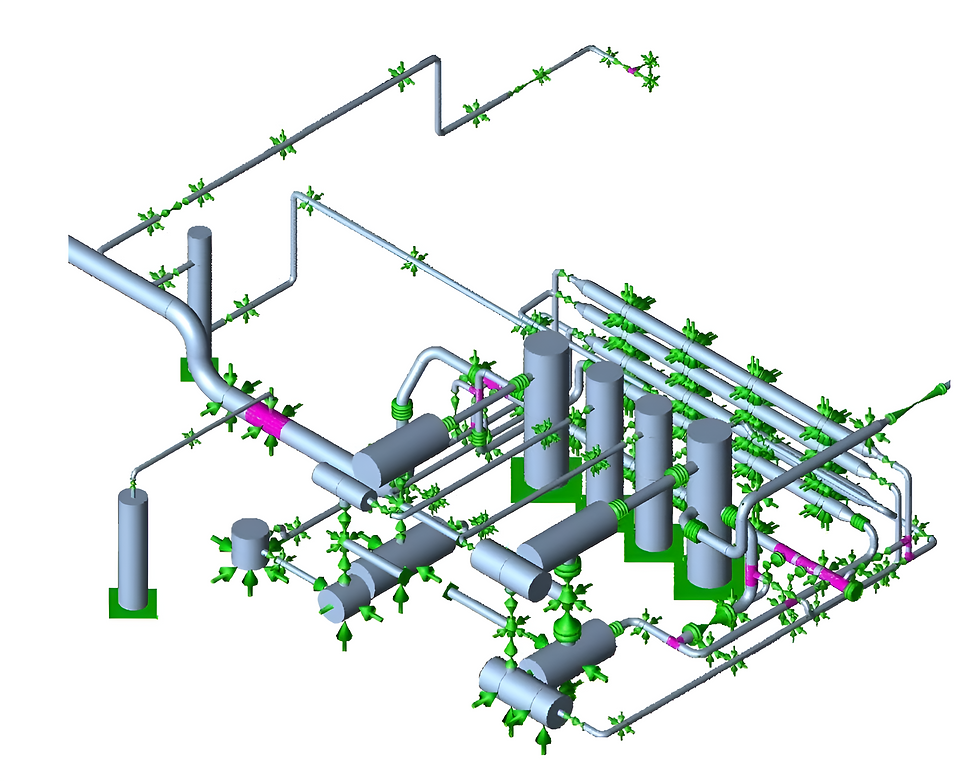
LPG HYDROGEN PIPING LAYOUT AND ROUTING
LPG Piping Design and Engineering Expertise
Divya Engineering’s approach to LPG system design encompasses a wide range of specialized services necessary for creating safe, efficient, and reliable transportation systems. A crucial phase of the design process is the Piping Layout and Routing stage, where the team ensures that LPG systems are engineered to meet operational performance standards while adhering to strict safety requirements. Efficient layout planning is especially critical in sectors like industrial manufacturing, energy, and fuel processing, where the safe and effective transport of LPG is vital to operations. The company focuses on optimizing system designs to enhance both safety and ease of maintenance.
To achieve optimal results, Divya Engineering employs cutting-edge tools to model, visualize, and meticulously plan LPG piping systems for maximum accuracy
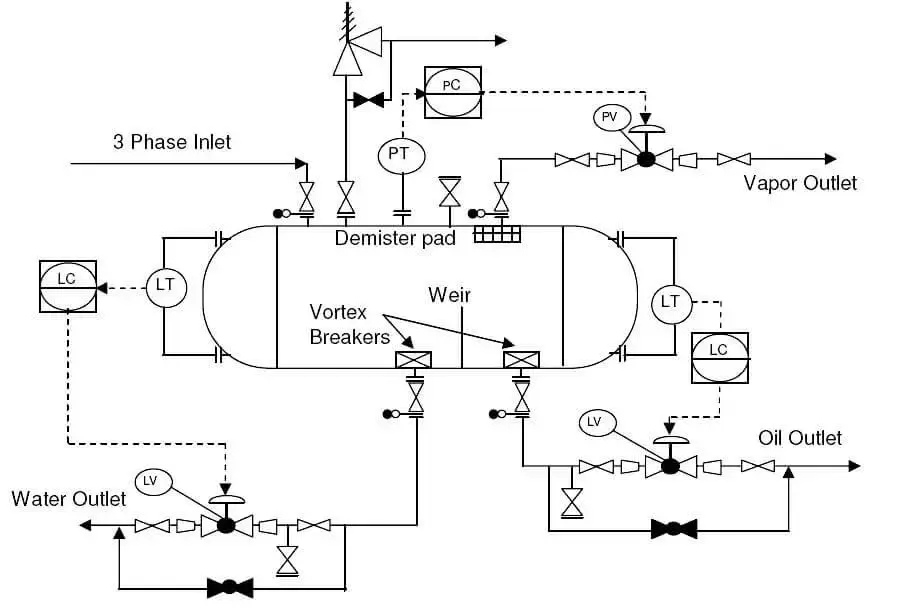
LPG PIPING SUPPORT DESIGN
Piping Support Design
Piping Support Design is a key element in LPG piping systems, addressing the structural integrity of systems that may be exposed to high pressures, temperatures, mechanical stresses, vibrations, and potentially corrosive conditions. Divya Engineering’s expertise lies in designing robust supports, hangers, and brackets that secure piping systems and minimize the risk of failure. Using advanced stress analysis tools like CAESAR II and AutoCAD Plant 3D, along with BIM technologies like Revit, the company ensures that LPG piping systems are resilient and durable, even under demanding operating conditions.

LPG PIPING MATERIAL SELECTION
Material Selection for LPG Systems
Material selection plays a crucial role in LPG system design to ensure long-term performance and reliability. Divya Engineering works closely with clients to select materials that can withstand the unique challenges presented by LPG, including extreme pressures, temperatures, and potential corrosive environments. Factors like pressure tolerance, temperature resistance, and corrosion resistance are carefully considered to ensure the system’s operational longevity and efficiency

LPG PIPING STRESS ANALYSIS
Piping Stress Analysis and Compliance
Piping stress analysis is essential for systems designed to transport LPG, as these systems must endure pressure surges, thermal expansion, and external mechanical loads. Divya Engineering performs in-depth stress evaluations to ensure that LPG piping systems are both durable and safe, using advanced software like CAESAR II to simulate and analyze stresses on the piping systems. Compliance with industry standards is of utmost importance, and Divya Engineering adheres to the following guidelines:
-
ASME B31.3: Governs the design of process piping systems, ensuring they can safely transport fluids such as LPG.
ASME B31.1: Covers power piping systems, including those used to transport high-pressure and high-temperature fluids like LPG

LPG PIPING AND INSTRUMENTATION DIAGRAMS (P&IDS):
P&IDs and Specification Development
Divya Engineering also provides comprehensive services in developing Piping and Instrumentation Diagrams (P&IDs) for hydrogen systems. These diagrams outline the layout and components of the piping system, including valves, pumps, instrumentation, and control systems. P&IDs are essential for simplifying maintenance and troubleshooting while ensuring safe operation. Additionally, Divya Engineering creates detailed piping specifications and standards that define the necessary parameters for installation, operation, and maintenance, ensuring compliance with both local and international safety and performance standards

LPG DEVELOPMENT OF PIPING SPECIFICATIONS AND STANDARDS
Divya Engineering offers services in developing Piping Specifications and Standards for high-pressure systems. They create detailed specifications and standards for piping materials, fabrication, and installation, ensuring consistency, quality, and compliance with industry regulations throughout the project lifecycle. ​Divya Engineering
Key Aspects of Their Piping Specifications and Standards Development:
-
Material Selection: Choosing appropriate materials based on factors such as fluid compatibility, operating temperature, pressure, and potential corrosion risks. ​Divya Engineering
-
Fabrication Guidelines: Establishing clear guidelines for the fabrication process to ensure that all components meet the required quality and performance standards.​
-
Installation Procedures: Developing standardized installation procedures to maintain consistency and quality across all aspects of the piping system.​
-
Compliance Assurance: Ensuring that all specifications and standards adhere to relevant industry codes and regulations, facilitating smooth project approvals and operational safety.
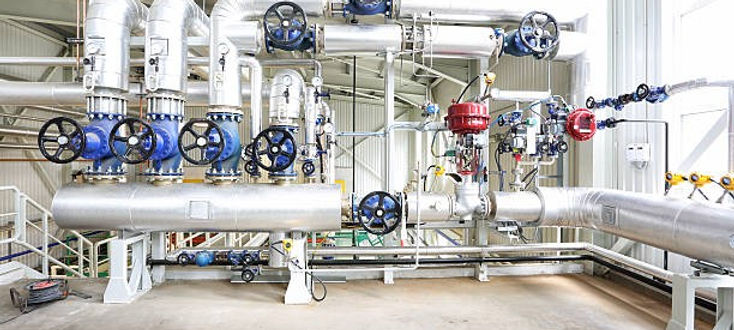
LPG PIPE SIZING AND HYDRAULIC CALCULATIONS
Advanced Modeling and Hydraulic Calculations
To optimize the efficiency and cost-effectiveness of LPG systems, Divya Engineering employs hydraulic calculations and advanced pipe-sizing techniques. These methods ensure that the system operates at peak performance while minimizing operational costs
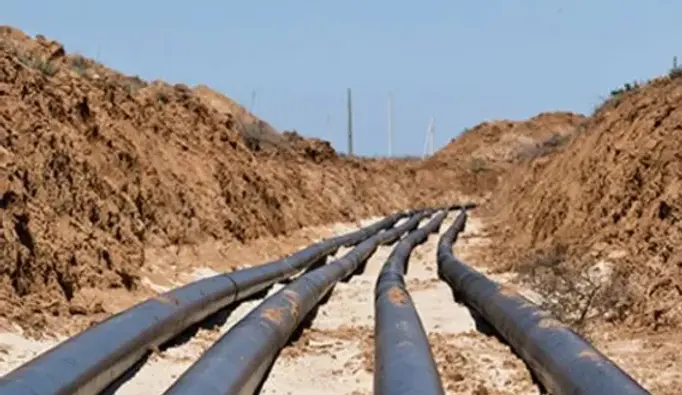
LPG 3D MODELING AND DESIGN
3D modeling technology, Divya Engineering provides highly accurate visual representations of LPG piping systems, improving planning accuracy, reducing errors, and ensuring more reliable construction outcomes. The 3D modeling process minimizes risks associated with rework and facilitates smoother transitions from design to construction.

LPG ISOMETRIC/FABRICATION/ERECTION DRAWINGS
Isometric, Fabrication, and Erection Drawings
Once the design phase is completed, Divya Engineering generates a comprehensive set of Isometric Drawings, Fabrication Drawings, and Erection Drawings. These drawings are essential for the precise construction and installation of LPG systems, ensuring that each component is fabricated, assembled, and installed according to the specifications. Isometric drawings provide a 3D perspective of the system, fabrication drawings detail the individual components and materials, and erection drawings guide the on-site assembly process, ensuring the final installation matches the original design.
LNG Piping Design Services
Piping Design Consultants- LNG Piping | Divya Engineering
Piping Design and Drafting: Creating detailed CAD drawings and design calculations for LNGpiping systems used in power plants, refineries, and other industrial facilities.
​
Pipe Stress Analysis: Performing static and dynamic stress analysis using software like CAESAR II to ensure the LNG piping system can withstand operational and environmental stresses.
​
3D Modeling and Design: Using software such as PDS, PDMS, or Auto Plant to create 3D models of LNG piping systems for better visualization and accuracy.
​
Isometric/Fabrication/Erection Drawings: Preparing detailed drawings for the fabrication and installation of LNG piping systems.
​
Support Detail Drawing Preparation: Designing and detailing the necessary supports for the LNG piping system to ensure stability and safety.
​
Project Management: Managing the entire LNG piping design project from initial conceptualization through fabrication and commissioning.
​
Compliance with Standards: Ensuring that the design complies with relevant standards such as ASME B31.1 for power piping and ASME B31.3 for process piping.
​
BILL OF MATERIAL, INSULATION & EXPANSION JOINTS
​
​
Challenges LNG piping design
​
Designing LNG (Liquefied Natural Gas) piping systems involves addressing several unique and complex challenges due to the cryogenic temperatures, flammability, and pressure requirements associated with LNG. Below are the key challenges in LNG piping system design:
1. Cryogenic Temperature Management:
LNG is transported and stored at extremely low temperatures (around -162°C or -258°F). At these temperatures, most materials become brittle and can fail under stress. Piping systems must be designed with materials that remain ductile and stable under cryogenic conditions. Common materials used for LNG piping include austenitic stainless steels and special alloys, which must be carefully selected for their ability to handle extreme cold without cracking. Proper insulation is also critical to minimize heat transfer and prevent the LNG from warming up and vaporizing (boil-off).
2. Thermal Insulation:
To prevent boil-off and maintain the LNG in its liquid state, it is essential to have highly effective insulation in place. LNG piping must be insulated to minimize heat gain from the environment, which can cause LNG to vaporize. Special insulation materials, such as polyurethane foam, fiberglass, or vacuum-insulated panels, are used to maintain cryogenic temperatures. However, designing these insulation systems for optimal performance and durability under varying environmental conditions remains a challenge, as they must also withstand external wear and corrosion over time.
3. Hydrostatic and Thermal Expansion:
LNG pipes experience both hydrostatic pressure (due to the liquid state of LNG) and thermal expansion due to temperature fluctuations. The cryogenic temperatures cause the piping to contract, while thermal exposure during normal operations can lead to expansion. Designers must account for these opposing forces by using flexible joints, expansion loops, and appropriate pipe supports to minimize the risk of stress fractures or joint failures.
4. Material Selection:
The materials used for LNG piping must be resistant to brittle fracture, fatigue, and hydrogen embrittlement, which can occur in the cryogenic environment. Stainless steel is a common choice, but it must be the correct grade to ensure resistance to low-temperature embrittlement and ensure longevity. Other materials like Inconel or copper alloys are sometimes used in specific applications, depending on the pressures and temperatures involved. Furthermore, materials need to be compatible with LNG’s properties, ensuring long-term integrity and safety.
5. Pressure and Flow Control:
LNG is typically transported under high pressure, requiring the design of pressure-control systems that can safely handle these conditions. The design must ensure that pressure levels remain within a safe operating range to prevent system failures or catastrophic accidents. Pressure relief valves, regulators, and flow meters must be accurately designed and sized to maintain safe pressure and flow levels. Designers also need to account for pressure fluctuations that can occur due to changes in temperature, LNG consumption rates, or pumping actions.
6. Flammability and Explosion Risks:
LNG is a highly flammable substance and poses a significant fire and explosion risk if not handled properly. While LNG itself is not explosive in its liquid state, it can vaporize quickly when exposed to heat and form a highly combustible gas mixture. This creates potential fire hazards if leaks occur, especially in confined or poorly ventilated spaces. Therefore, LNG piping systems must be designed with high-integrity seals, leak detection systems, and explosion-proof equipment. Additional safety measures, including emergency shutdown systems and venting systems, must be integrated to ensure safe operation in case of leaks or equipment failure.
7. Leak Prevention and Detection:
Given the flammable nature of LNG vapor, leak prevention and detection are paramount. Leaks in LNG piping systems can be dangerous, especially if they occur in confined spaces or near ignition sources. Piping systems need to be designed with tight seals and joints that can withstand the cold temperatures of LNG. Leak detection systems, such as hydrogen sensors, infrared gas detection, or pressure monitoring systems, must be incorporated to provide real-time monitoring for any signs of leakage. Designers also have to account for the small size of LNG molecules, which makes detection of minor leaks particularly difficult.
8. Vibration and Mechanical Stress:
Pumps, compressors, and other machinery used in LNG systems can generate vibrations that can cause mechanical stress on the piping system. These vibrations can lead to fatigue in the piping material, especially at weak points like joints, flanges, and supports. To prevent this, LNG piping systems require vibration-dampening features, such as flexible joints, proper pipe supports, and expansion loops to distribute mechanical stresses and minimize wear and tear.
9. Safety and Regulatory Compliance:
LNG piping systems must comply with stringent safety regulations and standards set by national and international authorities, including the American Society of Mechanical Engineers (ASME), National Fire Protection Association (NFPA), and others. These standards regulate the design, material selection, pressure and flow control, and safety measures to ensure that LNG systems operate without posing a threat to workers, the public, or the environment. Designers must be familiar with these regulations and integrate them into their system designs to ensure compliance throughout the project lifecycle.
10. Environmental Conditions and External Threats:
LNG piping systems are often exposed to challenging environmental conditions, such as high winds, flooding, or seismic activity. These environmental factors must be considered when designing the piping infrastructure. For example, in coastal or offshore locations, designers need to account for saltwater corrosion, while in earthquake-prone regions, the piping system must be designed to withstand seismic events without rupturing or failing. External threats such as third-party damage or physical impacts also require the incorporation of protective measures like reinforced pipelines or buried pipes to minimize risk.
11. Boil-Off Gas Management:
LNG is transported in a liquid state, but it inevitably vaporizes over time due to small temperature increases or during periods of high demand. The vaporized gas, known as boil-off gas (BOG), needs to be safely managed and directed. BOG recovery systems must be designed to capture and re-condense the gas or convert it back into a usable form, such as by directing it to power generation systems or flaring it off safely. Managing BOG efficiently is crucial to prevent waste and ensure that the LNG system operates at peak efficiency.
12. Cost Management:
Designing LNG systems can be capital intensive due to the need for specialized materials, insulation, and cryogenic equipment. Balancing cost with safety, reliability, and efficiency is a challenge. Designers must choose cost-effective solutions without compromising the integrity of the system. Additionally, maintaining cost-effective operations throughout the lifecycle of the LNG system is crucial, particularly in terms of energy efficiency, material durability, and system maintenance.
13. System Integration and Complexity:
LNG piping systems often need to integrate with various other systems, such as storage tanks, compressors, and LNG distribution networks. These complex systems require seamless integration to ensure that LNG is safely and efficiently transported, stored, and delivered. Designing for compatibility across various components and systems can be challenging, as it requires expertise in several different engineering disciplines, such as structural, mechanical, and electrical systems.
Conclusion:
LNG piping system design presents unique challenges that require specialized knowledge and expertise. The design process must address factors such as cryogenic temperatures, material compatibility, pressure control, leak prevention, and safety, all while ensuring compliance with stringent regulations. By carefully addressing these challenges with advanced engineering solutions, it is possible to create LNG piping systems that are safe, reliable, efficient, and cost-effective, capable of supporting the growing global demand for natural gas.
ChatGPT can make mistakes. Check important info.
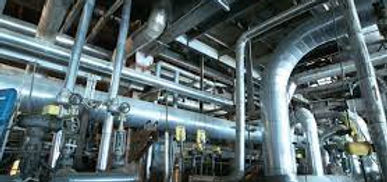

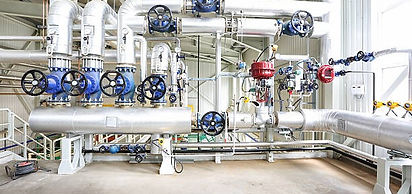
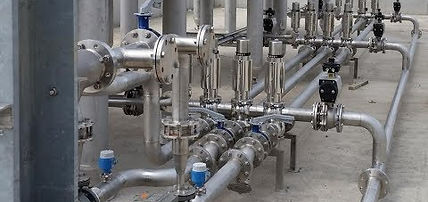