
DiVYA
PHONE : +91-8374485833,
Mail : storagetanks@mail.com
INDUSTRIAL PIPING DESIGN CONULTANCY SERVICES

Jacket Piping Design Services
Piping Design Engineering Services- Jacket Piping | Divya Engineering
Piping Design and Drafting: Creating detailed CAD drawings and design calculations for Jacket piping systems used in power plants, refineries, and other industrial facilities.
​
Pipe Stress Analysis: Performing static and dynamic stress analysis using software like CAESAR II to ensure the Jacket piping system can withstand operational and environmental stresses.
​
3D Modeling and Design: Using software such as PDS, PDMS, or Auto Plant to create 3D models of Jacket piping systems for better visualization and accuracy.
​
Isometric/Fabrication/Erection Drawings: Preparing detailed drawings for the fabrication and installation of Jacket piping systems.
​
Support Detail Drawing Preparation: Designing and detailing the necessary supports for the Jacket piping system to ensure stability and safety.
​
Project Management: Managing the entire Jacket piping design project from initial conceptualization through fabrication and commissioning.
​
Compliance with Standards: Ensuring that the design complies with relevant standards such as ASME B31.1 for power piping and ASME B31.3 for process piping.
​
BILL OF MATERIAL, INSULATION & EXPANSION JOINTS
​
​
Challenges in Jacket Piping Design
Jacket piping systems are essential for maintaining the temperature of fluids being transported through pipes, either by heating or cooling them through an outer jacket. These systems are widely used in industries such as chemical processing, pharmaceuticals, oil and gas, and power generation, where precise temperature control is crucial. However, designing jacket piping systems presents several challenges that require careful consideration. Below are some of the key challenges faced in jacket piping design:
1. Thermal Management and Efficiency
One of the primary purposes of jacketed piping is to regulate the temperature of the fluid inside the pipe. Achieving effective heat transfer between the inner pipe (the process pipe) and the jacket is essential. The challenge lies in optimizing the flow rate and temperature of the heating or cooling medium inside the jacket to ensure that the desired temperature is maintained consistently. If the heat transfer is inefficient, it can lead to temperature fluctuations or inadequate heating/cooling of the fluid, compromising system performance.
2. Material Selection
Selecting the appropriate materials for both the inner pipe and the jacket is crucial. The inner pipe must be compatible with the fluid being transported, while the jacket needs to withstand external factors such as pressure, temperature, and corrosion. The materials must also maintain their mechanical properties under high temperatures, as they will be subjected to thermal expansion and potential stresses. Furthermore, the inner and outer pipes must be compatible to avoid issues such as galvanic corrosion or differential expansion, which can cause leaks or failures.
3. Stress and Pressure Considerations
Jacket piping systems are subjected to both internal and external pressures. The inner pipe carries the process fluid under pressure, while the jacket carries a heating or cooling medium, which can also be pressurized. The challenge is ensuring that both pipes can withstand these pressures without failure. Additionally, thermal expansion due to temperature changes in both the inner pipe and the jacket needs to be accounted for. If not properly designed, the system may experience stress-induced issues such as buckling, pipe deformation, or leakage.
4. Space and Installation Constraints
Jacket piping systems typically require more space than standard piping systems due to the additional outer layer. The added size and complexity can present challenges in environments where space is limited or where the piping system needs to navigate tight areas. Proper routing and placement of jacketed pipes are critical to ensure that the system fits within the available space and does not interfere with other parts of the infrastructure. Installation of jacket piping also requires precision to maintain the correct clearances and avoid damage during the process.
5. Heat Loss and Insulation
While jacket piping is designed to regulate temperature, there is always some degree of heat loss, particularly in large systems or in colder environments. This heat loss can lead to inefficient energy use, increased operational costs, and compromised system performance. Proper insulation of the outer jacket is critical to minimize heat loss, but this must be carefully balanced with the need to ensure that the jacket pipe can maintain its structural integrity and heat transfer efficiency.
6. Flow Distribution in the Jacket
Achieving uniform flow distribution in the jacket is another challenge. The flow of heating or cooling fluid in the jacket should be evenly distributed around the process pipe to ensure consistent temperature control. Uneven distribution can lead to hot or cold spots, which may not provide the required heating or cooling along the length of the piping. Ensuring proper design and placement of inlet and outlet ports, as well as controlling the velocity and pressure of the fluid within the jacket, is critical to achieve uniform thermal regulation.
7. Leak Prevention and Monitoring
Like all piping systems, jacketed pipes are prone to the risk of leaks, particularly at joints or welds where the inner pipe and jacket are connected. Leaks in the jacket can lead to the escape of hazardous fluids, loss of temperature control, or contamination of the heating/cooling medium. Ensuring that the joints are properly sealed and tested is crucial for leak prevention. Additionally, integrating leak detection systems into the design of jacket piping systems helps monitor for any failures in real-time, adding an extra layer of safety.
8. System Integration and Complexity
Jacketed piping systems need to be integrated with other components of the overall process, such as pumps, valves, heat exchangers, and pressure regulators. Ensuring that all these components work together seamlessly requires detailed planning and design. The added complexity of managing the interaction between the process pipe and the jacket, as well as integrating the heating or cooling system into the larger process flow, requires a high level of engineering expertise. Any integration issues can lead to operational inefficiencies or system failures.
9. Maintenance and Inspection
Jacket piping systems often require ongoing maintenance and inspection to ensure their long-term performance. The inner pipe may be prone to corrosion or erosion due to the transported fluid, while the outer jacket can suffer from wear and tear from external environmental factors, such as pressure or temperature changes. Accessing the jacket for inspection and maintenance can also be more difficult than for single-wall systems. Regular monitoring, inspection, and maintenance are essential to keep the system in optimal working condition.
10. Compliance with Regulations and Standards
Jacket piping systems, especially in industries like chemicals, pharmaceuticals, and oil and gas, must adhere to strict safety, environmental, and operational standards. These regulations often define requirements for materials, pressure ratings, insulation, and safety features. Meeting these standards while optimizing the design for efficiency and cost-effectiveness can be challenging, but it is essential for ensuring compliance and ensuring the safety of the operation.
11. Cost Considerations
Jacketed piping systems inherently involve higher initial costs due to the additional materials, engineering complexity, and installation requirements. Balancing the need for a high-performance, durable system with cost constraints is a common challenge. Engineering teams must ensure that the benefits of using a jacket piping system—such as improved temperature control and reduced risk of fluid degradation—justify the additional cost while remaining within the project’s budget.
Conclusion
Designing jacket piping systems requires a detailed understanding of heat transfer, fluid dynamics, pressure considerations, and material selection. The challenges mentioned above necessitate careful planning, advanced engineering techniques, and close attention to detail to ensure that the final system is efficient, reliable, and safe. At Divya Design Consultancy, we are committed to addressing these challenges with innovative solutions, ensuring that your jacket piping system meets the highest standards of performance, safety, and cost-effectiveness.

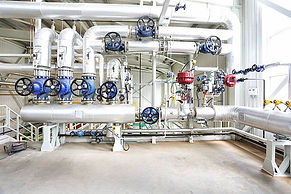

