
DiVYA
PHONE : +91-8374485833,
Mail : storagetanks@mail.com
INDUSTRIAL PIPING DESIGN CONULTANCY SERVICES

Instrument Air Piping Design Services
Piping Design engineering services Instrument Piping piping | Divya Engineering
Piping Design and Drafting: Creating detailed CAD drawings and design calculations for Instrument Air piping systems used in power plants, refineries, and other industrial facilities.
​
Pipe Stress Analysis: Performing static and dynamic stress analysis using software like CAESAR II to ensure the Instrument Air piping system can withstand operational and environmental stresses.
​
3D Modeling and Design: Using software such as PDS, PDMS, or Auto Plant to create 3D models ofInstrument Air piping systems for better visualization and accuracy.
​
Isometric/Fabrication/Erection Drawings: Preparing detailed drawings for the fabrication and installation of Instrument Air piping systems.
​
Support Detail Drawing Preparation: Designing and detailing the necessary supports for the Instrument Air piping system to ensure stability and safety.
​
Project Management: Managing the entire Instrument Air piping design project from initial conceptualization through fabrication and commissioning.
​
Compliance with Standards: Ensuring that the design complies with relevant standards such as ASME B31.1 for power piping and ASME B31.3 for process piping.
​
BILL OF MATERIAL, INSULATION & EXPANSION JOINTS
​
​
Challenges in Instrument Air Piping Design
Designing Instrument Air piping systems is a critical task for ensuring the proper functioning of pneumatic equipment, instruments, and control systems in various industrial sectors such as oil and gas, power generation, and chemical processing. While these systems are essential for operational efficiency and safety, there are several challenges associated with their design and implementation. Below are some of the key challenges in Instrument Air piping design:
1. Air Quality and Filtration
Instrument air must be clean, dry, and free from contaminants such as moisture, oil, and particulate matter. Ensuring that the air quality meets the stringent requirements of the system can be challenging. The design must include adequate filtration and drying systems, such as air dryers and filters, to prevent contamination that could damage instruments and control systems. Ensuring continuous, reliable air quality over the system’s lifecycle requires careful planning and monitoring.
2. System Sizing and Pressure Requirements
Properly sizing the piping system to handle the required air flow and pressure is a critical aspect of the design. Instrument air systems must provide consistent and reliable air supply to instruments and control devices, which can be sensitive to pressure fluctuations. Calculating the correct pipe diameters, choosing the right materials, and determining the appropriate number and size of compressors and receivers is essential to maintain the desired pressure throughout the system and avoid over or under-sizing issues. Incorrect sizing can result in inefficiencies, excessive energy consumption, or inadequate pressure supply.
3. Air Compressors and Storage
Instrument air systems require reliable, high-performance air compressors to generate the required air pressure. The design challenge is selecting the appropriate type of compressor, whether it's rotary screw, reciprocating, or centrifugal, and ensuring that it can meet the demands of the system efficiently. Additionally, storage tanks (receivers) are necessary to maintain a stable pressure in the system. Proper integration of the compressors, storage tanks, and piping is required to ensure that air is supplied at a consistent pressure, and the compressors are not overloaded.
4. Temperature and Moisture Control
Compressed air, when generated, often has a higher temperature and contains moisture. If the air is not properly cooled or dried before being delivered to the instruments, the moisture can condense inside the pipes, leading to blockages, corrosion, or damage to sensitive equipment. Designing the system with appropriate cooling and moisture separation mechanisms, such as aftercoolers and separators, can be challenging. Additionally, ensuring that these systems are regularly maintained to prevent moisture buildup and maintain air quality requires careful planning.
5. Piping Material Selection
Instrument air piping must be constructed from materials that are resistant to corrosion, wear, and leakage, especially in harsh environments. Materials such as carbon steel, stainless steel, or plastic may be used, depending on the operational conditions. The challenge lies in selecting materials that are compatible with the specific air quality requirements, pressure ratings, and temperature conditions while also being cost-effective. Additionally, the material must be resistant to the buildup of contaminants like scale or rust, which could degrade the quality of the air and affect system performance.
6. Leakage and Maintenance
Leaks in instrument air systems can lead to significant operational issues, including pressure drops, energy waste, and equipment malfunction. Designing for leak prevention is crucial, and it requires selecting the right fittings, joints, and seals, and ensuring proper installation techniques. In addition, regular inspection and maintenance schedules must be factored into the design to ensure the longevity and reliability of the system. Ensuring easy access to the piping for inspection and maintenance without disrupting operations is also a key challenge.
7. Pressure Relief and Safety Considerations
Instrument air systems must be equipped with appropriate safety measures, including pressure relief valves and safety valves, to prevent over-pressurization. Over-pressurization can lead to catastrophic failure of the system or damage to sensitive equipment. Designing the system to handle pressure fluctuations and ensuring that all components are designed to withstand maximum pressure loads without failure is a critical aspect of the design.
8. Energy Efficiency
Energy consumption is a major consideration when designing instrument air systems. Compressed air systems are often energy-intensive, and ensuring that the system is as energy-efficient as possible is essential to reduce operational costs. This can involve selecting energy-efficient compressors, minimizing pressure drops, and optimizing pipe sizes to reduce friction losses. Additionally, using energy recovery systems or pressure reduction techniques can help improve overall efficiency.
9. System Integration with Other Equipment
Instrument air systems are typically integrated with a range of other industrial systems, including control valves, actuators, and other pneumatic instruments. Ensuring proper integration and coordination between the instrument air piping and other components of the plant or facility is a significant challenge. This includes maintaining consistent air pressure and quality, ensuring compatibility with other control systems, and preventing cross-contamination between different systems.
10. Compliance with Standards and Regulations
Instrument air systems must comply with various safety, regulatory, and environmental standards, including ASME, ANSI, and local safety codes. These regulations define acceptable standards for air quality, pressure levels, safety measures, and materials. Ensuring that the system design meets these codes while optimizing performance can be challenging, particularly when dealing with complex or highly regulated industries such as petrochemical or pharmaceutical sectors.
11. Space Constraints and Installation
In many industrial environments, space for installing piping systems can be limited, and instrument air piping must be designed to fit within these space constraints. Proper routing of the pipes, careful placement of compressors and receivers, and effective use of vertical and horizontal space are necessary to avoid conflicts with other systems or physical barriers. The installation process also requires precision to ensure proper alignment, adequate support, and sufficient access for maintenance.
12. Redundancy and Reliability
Instrument air systems are crucial for the operation of control systems and instruments in critical processes. Therefore, ensuring system reliability and minimizing the risk of downtime is paramount. Designing the system with redundancy, such as multiple compressors or backup systems, is essential to ensure uninterrupted air supply. Identifying and mitigating potential points of failure and incorporating fail-safe mechanisms is a critical aspect of the design process.
Conclusion
Designing instrument air piping systems involves addressing a variety of technical and practical challenges, from maintaining air quality and pressure consistency to optimizing energy efficiency and ensuring compliance with safety standards. By carefully considering each of these challenges and employing innovative solutions, Divya Design Consultancy helps clients develop reliable, safe, and cost-effective instrument air systems. Our expertise and commitment to excellence ensure that each project is completed to the highest standards, optimizing the performance and reliability of the instrument air supply system.


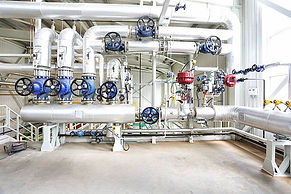
