
DiVYA
PHONE : +91-8374485833,
Mail : storagetanks@mail.com
INDUSTRIAL PIPING DESIGN CONULTANCY SERVICES

High Temperature Piping design services
Piping Design Consultancy Services- High Temperature Piping | Divya Engineering
Piping Design and Drafting: Creating detailed CAD drawings and design calculations for High Temperature piping systems used in power plants, refineries, and other industrial facilities.
​
Pipe Stress Analysis: Performing static and dynamic stress analysis using software like CAESAR II to ensure the High Temperature piping system can withstand operational and environmental stresses.
​
3D Modeling and Design: Using software such as PDS, PDMS, or Auto Plant to create 3D models of High Temperature piping systems for better visualization and accuracy.
​
Isometric/Fabrication/Erection Drawings: Preparing detailed drawings for the fabrication and installation of High Temperature piping systems.
​
Support Detail Drawing Preparation: Designing and detailing the necessary supports for the High Temperature piping system to ensure stability and safety.
​
Project Management: Managing the entire High Temperature piping design project from initial conceptualization through fabrication and commissioning.
​
Compliance with Standards: Ensuring that the design complies with relevant standards such as ASME B31.1 for power piping and ASME B31.3 for process piping.
​
BILL OF MATERIAL, INSULATION & EXPANSION JOINTS
​
​
Challenges in High-Temperature Piping Design
Designing high-temperature piping systems presents a unique set of challenges due to the extreme conditions these systems must endure. High-temperature piping is typically used in industries such as power generation, petrochemicals, chemical processing, and metal production, where heat, pressure, and aggressive environments are commonplace. Here are the key challenges involved in high-temperature piping design:
1. Material Selection
High-temperature piping systems are subjected to extreme heat, which can cause materials to degrade over time. Selecting the right materials is critical to ensure that the piping can withstand high temperatures without failing. The materials must have high thermal resistance, be resistant to oxidation and corrosion, and maintain structural integrity at elevated temperatures. Common materials used for high-temperature piping include alloys like stainless steel, carbon steel, and special alloys. Ensuring the material’s longevity while maintaining cost-effectiveness is a complex challenge.
2. Thermal Expansion and Contraction
As temperatures rise, piping systems undergo thermal expansion, which can result in significant dimensional changes. If not properly managed, thermal expansion can lead to high levels of stress, strain, and potential damage to the piping, joints, or supports. Designing the system to accommodate thermal expansion through expansion joints, bellows, and properly placed supports is crucial for maintaining the structural integrity and operational efficiency of the piping system.
3. Stress and Fatigue
High-temperature piping systems are subject to both thermal and mechanical stresses. Continuous exposure to high temperatures can cause materials to weaken, leading to creep (slow deformation under stress), fatigue, and ultimately, failure. Engineers must conduct detailed stress analysis to identify areas prone to failure and ensure that the system is designed to handle long-term exposure to elevated temperatures without compromising safety or performance.
4. Corrosion and Erosion
High-temperature piping systems, especially those carrying corrosive fluids or gases, face significant risks from both corrosion and erosion. High temperatures can accelerate the rate of oxidation and corrosion, leading to material degradation. Piping systems must be designed with protective coatings, corrosion-resistant alloys, and proper insulation to minimize these risks. Erosion from the high-speed flow of fluids or gases can also weaken the system over time. Selecting appropriate materials and considering the operating conditions are essential to mitigating these risks.
5. Pressure and Temperature Relationship
High-temperature systems often operate under high pressure, and the interaction between temperature and pressure can complicate design. As temperature increases, the material properties of the piping may change, affecting the system’s ability to handle pressure. For example, steel becomes less resistant to pressure at high temperatures. Careful design and analysis are necessary to ensure that the piping can safely handle both the temperature and pressure requirements.
6. Heat Loss and Insulation
High-temperature piping systems can result in significant heat loss if not properly insulated. Heat loss can reduce system efficiency and increase operational costs. In addition to designing the system for optimal heat transfer, insulation is required to retain heat and protect surrounding areas from excessive heat exposure. Selecting the right insulation material and design is key to improving energy efficiency and reducing costs.
7. Welding and Fabrication Challenges
The high temperatures involved in these systems can create difficulties during welding and fabrication. High-temperature materials, especially alloys, may be more challenging to weld, requiring specialized techniques and expertise. Proper welding techniques must be employed to ensure the integrity of the joints and avoid issues such as cracking, distortion, or weakening of the material.
8. Vibration and Thermal Cycles
Piping systems exposed to fluctuating temperatures experience thermal cycling—periodic heating and cooling—which can cause expansion and contraction. These thermal cycles can result in vibrations and mechanical stresses that contribute to wear and tear on the system. The design must account for these thermal cycles and incorporate vibration-dampening solutions and expansion joints to minimize stress on the system.
9. Safety Considerations
The combination of high temperatures and pressure makes high-temperature piping systems potentially hazardous if not designed and maintained properly. The risks of leaks, ruptures, or catastrophic failures can have serious safety and environmental implications. Therefore, the system must be designed with safety valves, pressure relief systems, and thorough monitoring to ensure that the piping can handle any abnormal conditions without failure.
10. Code Compliance and Standards
High-temperature piping systems must comply with industry standards, codes, and regulations to ensure safety, reliability, and efficiency. These codes, such as ASME, ASNI, and API, outline the required specifications for materials, design, and testing. Ensuring compliance with these standards while maintaining cost-effectiveness and meeting the specific requirements of each project can be a challenging balancing act.
11. Lifecycle Considerations
High-temperature piping systems are often used in environments where they will be exposed to extreme conditions for many years. The system’s design must take into account the anticipated lifecycle, including the potential for wear and tear, corrosion, and other factors that might affect its long-term performance. Incorporating redundancy, regular inspection schedules, and upgrade options into the design is essential for ensuring that the system operates safely and efficiently throughout its service life.
In conclusion, designing high-temperature piping systems requires a comprehensive understanding of material science, thermal dynamics, fluid mechanics, and safety engineering. Each project must be approached with care and precision to address the unique challenges that high-temperature environments present. At Divya Design Consultancy, we are committed to delivering high-temperature piping solutions that prioritize safety, durability, and efficiency, while adhering to the highest industry standards.
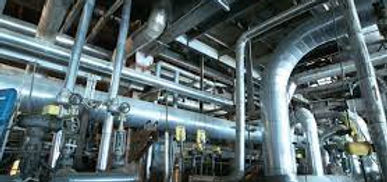
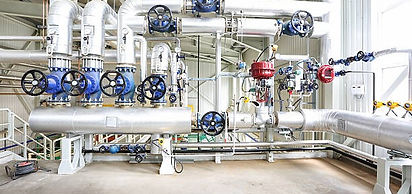

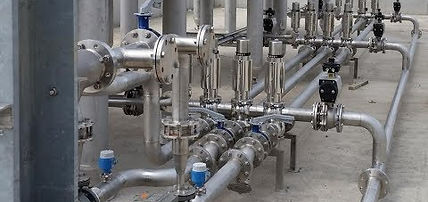