
DiVYA
PHONE : +91-8374485833,
Mail : storagetanks@mail.com
INDUSTRIAL PIPING DESIGN CONULTANCY SERVICES
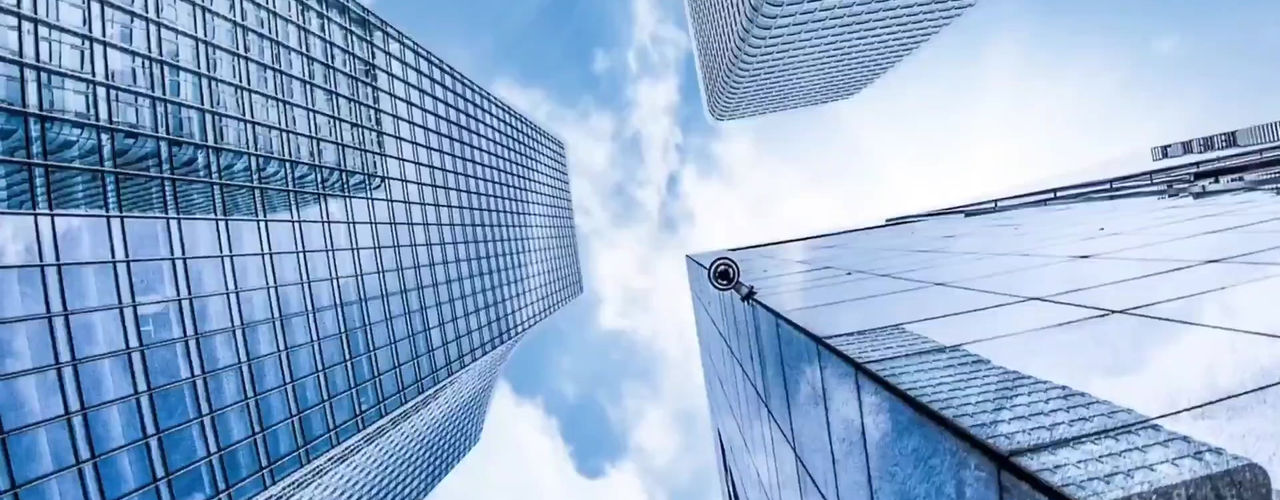
High pressure Piping Design Services
Piping Design Consultants- High Pressure Piping | Divya Engineering
"Divya Engineering offers expert piping design consultancy services specializing in high pressure piping systems. We provide innovative and cost-effective solutions tailored to your project needs
High-pressure piping refers to piping systems that are designed to handle fluids (liquids or gases) at high pressures. These systems are common in industries such as oil and gas, power generation, chemical manufacturing, and many other industrial applications where fluids need to be transported or processed under extreme pressure.
Key considerations when dealing with high-pressure piping include:
1. Material Selection
-
Strength & Durability: High-pressure systems require materials with high tensile strength, resistance to corrosion, and toughness under extreme conditions. Common materials include carbon steel, stainless steel, and sometimes alloys like Inconel or titanium.
-
Temperature Resistance: Some systems also deal with high temperatures, so materials must be chosen for both pressure and thermal properties.
2. Design Codes and Standards
-
High-pressure piping systems must be designed according to specific standards and codes such as ASME B31.3 (for Process Piping), ASME B31.1 (for Power Piping), and ASME Boiler and Pressure Vessel Code (BPVC). These codes define the requirements for materials, pressure ratings, testing, safety, and installation procedures.
3. Pressure Rating
-
Pressure Class: Pipes are rated according to their ability to withstand a certain amount of internal pressure. For high-pressure piping, pressure ratings could range from several hundred to several thousand psi (pounds per square inch), depending on the system’s design.
-
Burst Pressure: The pressure at which the pipe will fail or rupture. This is a critical factor for ensuring safety in high-pressure systems.
4. Safety
-
Stress Analysis: High-pressure systems are subject to high stresses that can lead to fatigue, leaks, or failure over time. Finite element analysis (FEA) is often used to simulate the behavior of piping under high-pressure conditions.
-
Pressure Relief Systems: Safety valves and pressure relief systems are essential in preventing overpressure situations that could result in catastrophic failure.
-
Weld Integrity: Welding techniques used to join high-pressure pipes are critical to ensuring strength and sealing under pressure. Non-destructive testing (NDT) such as ultrasonic testing or radiography is often used to detect flaws in the welds.
5. Piping Components
-
Valves: High-pressure valves must be robust and designed to handle high-flow rates and extreme conditions. They are often designed with specific features like double block and bleed, and sometimes even automatic shutoff to prevent overpressure.
-
Fittings and Flanges: Fittings like elbows, tees, and reducers, as well as flanges, need to be rated for the high-pressure conditions. They must be compatible with the material of the pipe to prevent failure at the joints.
-
Expansion Loops: High-pressure systems may experience thermal expansion, and expansion loops or bellows can be used to accommodate this.
6. Testing and Inspection
-
Hydrostatic Testing: After installation, high-pressure piping is usually tested with water (instead of the actual fluid) at pressures higher than normal operating conditions to ensure the system can handle the pressure safely.
-
Leak Testing: To verify the system's integrity and prevent leaks, various leak testing methods such as air testing or helium leak detection may be used.
7. Applications
-
Oil and Gas: High-pressure pipelines are used to transport natural gas, oil, or other fluids over long distances.
-
Power Plants: High-pressure steam is a critical part of power generation systems, especially in thermal and nuclear power plants.
-
Chemical & Petrochemical Industry: High-pressure reactors and pipelines are used for chemical processes that require high pressures for reactions to occur.
PIPING DESIGN AND DRAFTING
Yes, Divya Engineering offers comprehensive services in high-pressure piping design and drafting. Their expertise encompasses various aspects of piping systems, including those operating under high-pressure conditions. Specific services provided include:​
​
-
Piping Design and Drafting: Creating detailed CAD drawings and design calculations for various types of piping systems, including those in oil and gas, petrochemicals, power plants, and water storage tanks
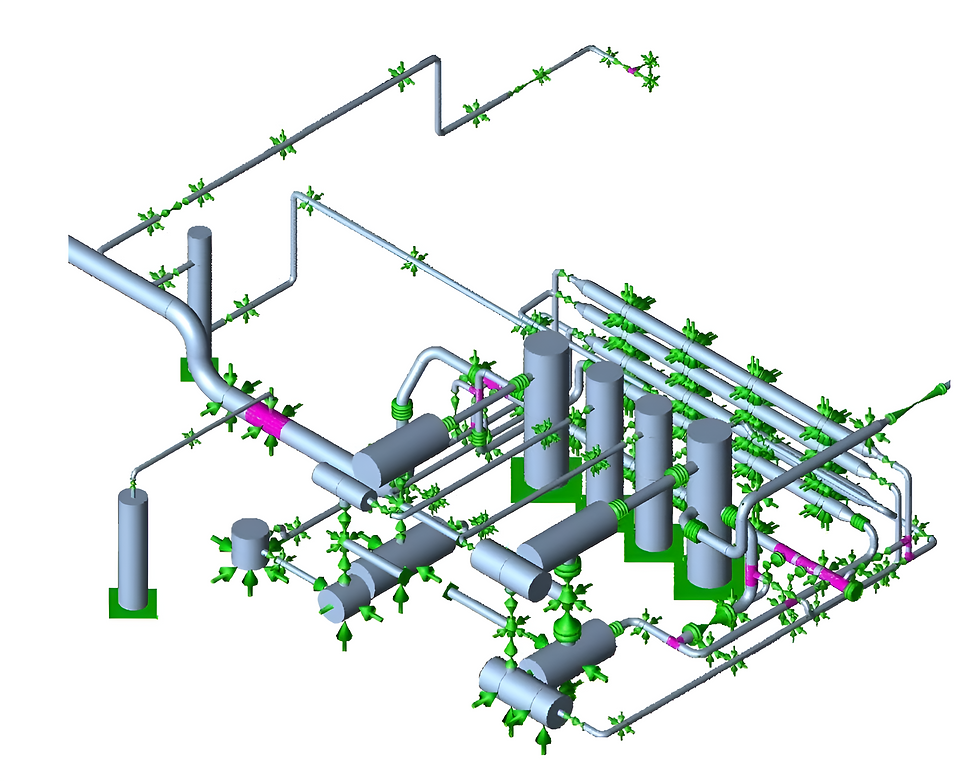
PIPING LAYOUT AND ROUTING
Divya Engineering provides specialized services in Piping Layout and Routing for high-pressure piping systems. Their expertise includes determining optimal layouts to ensure efficient flow, minimize pressure drops, and avoid interference with other equipment or structures. ​Divya Engineering
Key Aspects of Their Piping Layout and Routing Services:
-
Efficient Flow Design: Strategically planning pipe routes to facilitate smooth fluid movement, reducing energy losses and enhancing system performance.​
-
Pressure Drop Minimization: Designing layouts that minimize resistance to flow, thereby reducing pressure losses and improving overall efficiency.​
-
Conflict Avoidance: Ensuring that the piping design does not clash with existing equipment, structures, or other utilities, thereby simplifying installation and maintenance.​
-
Compliance with Standards: Adhering to industry standards and regulations to ensure safety, reliability, and regulatory compliance in all design aspects.
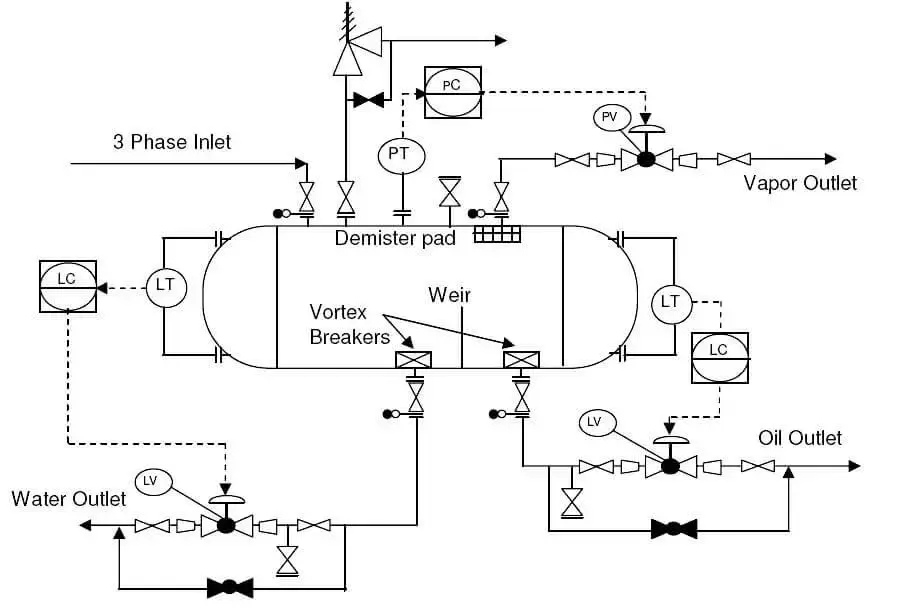
PIPING SUPPORT DESIGN
Divya Engineering offers specialized services in Piping Support Design for high-pressure piping systems. Their expertise includes designing and specifying supports to properly secure and stabilize the piping system, preventing excessive stress and vibration. ​Divya Engineering
Key Aspects of Their Piping Support Design Services:
-
Support Detail Drawing Preparation: Developing detailed drawings for supports to ensure the stability and safety of the piping system. ​Divya Engineering
-
Stress and Vibration Control: Designing supports that effectively manage thermal expansion, pressure-induced stresses, and vibrations, thereby maintaining the integrity of the system.​
-
Compliance with Standards: Ensuring that all support designs adhere to relevant industry standards and regulations, such as ASME B31.1 and ASME B31.3, to guarantee safety and reliability.

PIPING MATERIAL SELECTION
Divya Engineering provides comprehensive Piping Material Selection services for high-pressure systems. Their approach involves selecting appropriate pipe materials based on factors such as the fluid being transported, operating temperature and pressure, and corrosion considerations. ​Divya Engineering
Key Aspects of Their Piping Material Selection Services:
-
Fluid Compatibility: Choosing materials that are compatible with the specific fluids to prevent corrosion, erosion, or chemical reactions that could compromise the system's integrity.​
-
Operating Conditions: Assessing temperature and pressure conditions to select materials that can withstand the thermal and mechanical stresses encountered during operation.​
-
Corrosion Resistance: Evaluating environmental factors to select materials with appropriate corrosion resistance, ensuring the longevity and reliability of the piping system.

PIPING STRESS ANALYSIS
Divya Engineering offers comprehensive Piping Stress Analysis services as part of their high-pressure piping design solutions. They perform both static and dynamic stress analyses using advanced software like CAESAR II to ensure that piping systems can withstand operational and environmental stresses. ​
​
Piping stress analysis is crucial in the design phase, as it helps identify potential issues related to thermal expansion, pressure fluctuations, and mechanical loads. By simulating various operating conditions, engineers can optimize the design to prevent failures and enhance the system's reliability.​
​
For more detailed information or to discuss specific project requirements, you can contact Divya Engineering directly by phone at +91-9553747757.

PIPING AND INSTRUMENTATION DIAGRAMS (P&IDS):
Divya Engineering offers comprehensive services in developing Piping and Instrumentation Diagrams (P&IDs) as part of their high-pressure piping design solutions. P&IDs are essential for illustrating the piping system, including components, instrumentation, and control systems, providing a clear and detailed representation of the process flow and control mechanisms. ​Divya Engineering
Key Aspects of Their P&ID Services:
-
Detailed Representation: Creating precise diagrams that depict all piping components, instrumentation, and control systems to ensure clarity in design and operation.​
-
Process Understanding: Developing P&IDs that enhance the understanding of process flows, aiding in troubleshooting, maintenance, and optimization of the system.​
-
Compliance and Standards: Ensuring that all P&ID drawings adhere to relevant industry standards and regulations, facilitating smooth project approvals and operational safety.

DEVELOPMENT OF PIPING SPECIFICATIONS AND STANDARDS
Divya Engineering offers services in developing Piping Specifications and Standards for high-pressure systems. They create detailed specifications and standards for piping materials, fabrication, and installation, ensuring consistency, quality, and compliance with industry regulations throughout the project lifecycle. ​Divya Engineering
Key Aspects of Their Piping Specifications and Standards Development:
-
Material Selection: Choosing appropriate materials based on factors such as fluid compatibility, operating temperature, pressure, and potential corrosion risks. ​Divya Engineering
-
Fabrication Guidelines: Establishing clear guidelines for the fabrication process to ensure that all components meet the required quality and performance standards.​
-
Installation Procedures: Developing standardized installation procedures to maintain consistency and quality across all aspects of the piping system.​
-
Compliance Assurance: Ensuring that all specifications and standards adhere to relevant industry codes and regulations, facilitating smooth project approvals and operational safety.
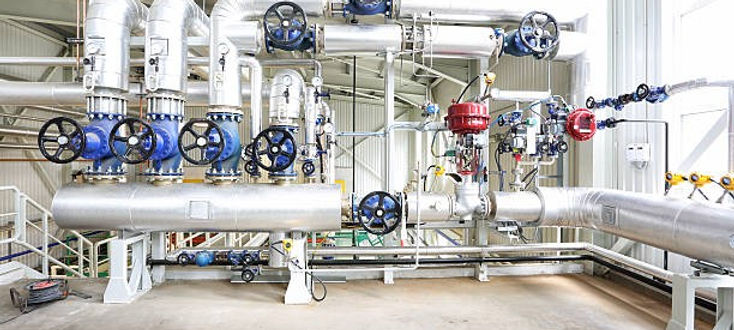
​PIPE SIZING AND HYDRAULIC CALCULATIONS
Divya Engineering offers Pipe Sizing and Hydraulic Calculations services for high-pressure systems. They calculate appropriate pipe sizes and perform hydraulic analyses to ensure desired flow rates and pressure drops, optimizing system efficiency and performance. ​Divya Engineering
Key Aspects of Their Services:
-
Pipe Sizing: Determining optimal pipe diameters to handle specific flow rates while minimizing material costs and energy losses.​
-
Hydraulic Analysis: Evaluating pressure drops and flow characteristics using established equations like Darcy-Weisbach and Hazen-Williams to design efficient piping systems.
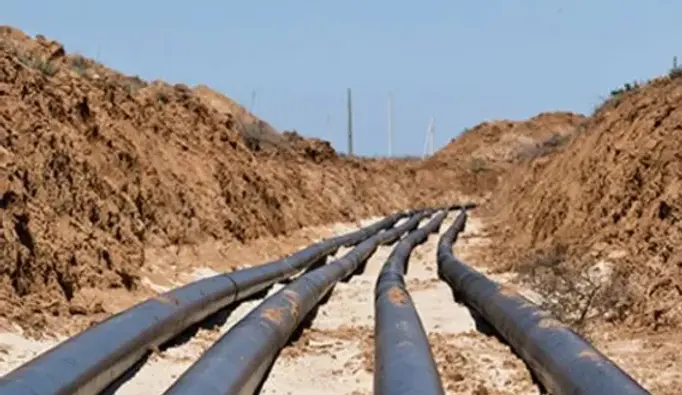
3D MODELING AND DESIGN
Divya Engineering offers 3D Modeling and Design services for high-pressure piping systems. We utilize advanced software such as PDS, PDMS, and Auto Plant to create detailed 3D models, enhancing visualization and accuracy in their designs. ​
Benefits of Their 3D Modeling and Design Services:
-
Enhanced Visualization: 3D models provide a clear representation of the piping system, aiding in understanding complex designs and facilitating better decision-making.​
-
Improved Accuracy: Utilizing advanced modeling software helps in detecting and resolving potential design conflicts early in the process, reducing errors during implementation.
-
Efficient Collaboration: Detailed 3D models serve as effective communication tools among project stakeholders, ensuring alignment and streamlining project workflows.

ISOMETRIC/FABRICATION/ERECTION DRAWINGS
Divya Engineering offers comprehensive services in preparing Isometric, Fabrication, and Erection Drawings for high-pressure piping systems. These detailed drawings are essential for the accurate fabrication and installation of piping systems, ensuring that all components fit together seamlessly during construction. ​Divya Engineering
Key Aspects of Their Drawing Services:
-
Isometric Drawings: Providing clear representations of piping systems, highlighting dimensions and spatial relationships, which are crucial for accurate fabrication and assembly.​
-
Fabrication Drawings: Delivering detailed drawings that outline the specifications and dimensions of each piping component, facilitating precise manufacturing processes.​
-
Erection Drawings: Creating comprehensive plans that guide the on-site assembly of piping systems, ensuring correct placement and integration with existing structures.
High Pressure Piping design services
Piping Design Consultants- High Pressure Piping | Divya Engineering
Piping Design and Drafting: Creating detailed CAD drawings and design calculations for steam piping systems used in power plants, refineries, and other industrial facilities.
​
Pipe Stress Analysis: Performing static and dynamic stress analysis using software like CAESAR II to ensure the steam piping system can withstand operational and environmental stresses.
​
3D Modeling and Design: Using software such as PDS, PDMS, or Auto Plant to create 3D models of steam piping systems for better visualization and accuracy.
​
Isometric/Fabrication/Erection Drawings: Preparing detailed drawings for the fabrication and installation of steam piping systems.
​
Support Detail Drawing Preparation: Designing and detailing the necessary supports for the steam piping system to ensure stability and safety.
​
Project Management: Managing the entire steam piping design project from initial conceptualization through fabrication and commissioning.
​
Compliance with Standards: Ensuring that the design complies with relevant standards such as ASME B31.1 for power piping and ASME B31.3 for process piping.
​
BILL OF MATERIAL, INSULATION & EXPANSION JOINTS
​
​
Challenges in Steam Piping Design
Challenges in High-Pressure Piping Systems
Designing and maintaining high-pressure piping systems presents numerous challenges due to the complexity, risks, and precision required in their execution. These challenges are particularly evident in industries like oil and gas, power generation, chemical processing, and other heavy industries where high-pressure systems are critical to operations. Here are some of the key challenges faced in high-pressure piping design and management:
-
Material Selection and Durability
High-pressure piping systems are exposed to extreme conditions, including high temperatures, corrosive environments, and mechanical stresses. Selecting the right materials that can withstand these conditions while ensuring longevity and safety is a significant challenge. Materials must not only resist pressure but also be resistant to corrosion, fatigue, and wear over time. -
Pressure Resistance and Safety
One of the biggest concerns in high-pressure systems is ensuring that the piping can safely handle the intended pressure without risk of failure. This requires accurate pressure analysis, including the consideration of pressure surges, vibration, and thermal expansion. The potential risks of a pressure-related failure—such as leaks, explosions, or catastrophic system breakdowns—demand meticulous design and regular maintenance. -
Thermal Expansion and Contraction
High-pressure piping systems are often subjected to temperature fluctuations that lead to thermal expansion and contraction. Managing this expansion is essential to preventing stress and damage to the pipes. Expansion joints, supports, and proper routing must be carefully designed to accommodate these changes while maintaining the integrity of the system. -
Stress Analysis and Fatigue Resistance
Piping systems under high pressure are subjected to significant mechanical stresses, both from the internal fluid pressure and external forces such as wind, seismic activity, and operational vibrations. Stress analysis and fatigue resistance are critical to ensuring the system's structural integrity over its operational life. Improperly designed or maintained systems are vulnerable to stress fractures, which can lead to leaks or failures. -
Regulatory Compliance
High-pressure piping systems are subject to strict industry regulations and safety standards. Compliance with national and international codes, such as ASME, ASNI, and API, is essential to ensure the safety, reliability, and environmental sustainability of the system. Navigating these codes and keeping up with regulatory changes can be a complex and time-consuming task. -
Leakage Prevention
High-pressure systems are highly susceptible to leaks, which can pose serious safety, environmental, and operational risks. Ensuring tight seals, proper welding, and high-quality material selection are essential for preventing leaks. Leak detection systems, monitoring, and regular inspections are also vital components in managing these risks. -
Design Optimization
Achieving a balance between efficiency, cost-effectiveness, and performance is a challenging task. Over-designing systems can lead to unnecessary costs, while under-designing can compromise safety and functionality. Optimizing the layout, material usage, and pipe sizing is key to developing a reliable system without overburdening the budget. -
Installation and Maintenance
The installation and maintenance of high-pressure piping systems require a high level of expertise and precision. Installation errors or poor welding techniques can lead to weak points in the system that may fail under pressure. Additionally, maintaining high-pressure systems involves regular inspections, monitoring for signs of wear or corrosion, and performing timely repairs to avoid system breakdowns. -
Environmental Factors
Environmental considerations, such as corrosive environments, seismic activity, temperature extremes, or the presence of hazardous chemicals, add another layer of complexity to high-pressure piping design. The system must be designed to accommodate these factors, using appropriate protective coatings, reinforcements, and monitoring systems to prevent failure. -
System Integration
High-pressure piping systems must often be integrated with other parts of an industrial infrastructure, including pumps, valves, and reactors. Ensuring smooth integration while maintaining the performance and safety of the entire system is a complex challenge. It requires detailed planning and coordination across multiple disciplines of engineering.
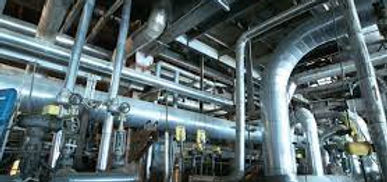
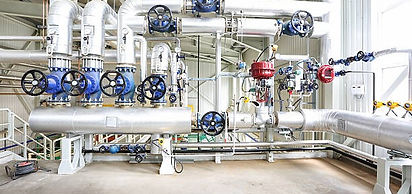

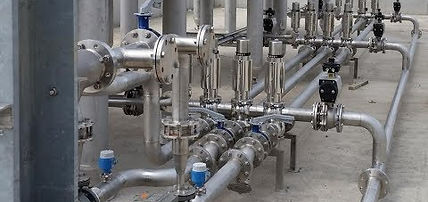