
DiVYA
PHONE : +91-8374485833,
Mail : storagetanks@mail.com
INDUSTRIAL PIPING DESIGN CONULTANCY SERVICES

High Pressure Piping design services
Piping Design Engineering Services- High Pressure Piping | Divya Engineering
Piping Design and Drafting: Creating detailed CAD drawings and design calculations for steam piping systems used in power plants, refineries, and other industrial facilities.
​
Pipe Stress Analysis: Performing static and dynamic stress analysis using software like CAESAR II to ensure the steam piping system can withstand operational and environmental stresses.
​
3D Modeling and Design: Using software such as PDS, PDMS, or Auto Plant to create 3D models of steam piping systems for better visualization and accuracy.
​
Isometric/Fabrication/Erection Drawings: Preparing detailed drawings for the fabrication and installation of steam piping systems.
​
Support Detail Drawing Preparation: Designing and detailing the necessary supports for the steam piping system to ensure stability and safety.
​
Project Management: Managing the entire steam piping design project from initial conceptualization through fabrication and commissioning.
​
Compliance with Standards: Ensuring that the design complies with relevant standards such as ASME B31.1 for power piping and ASME B31.3 for process piping.
​
BILL OF MATERIAL, INSULATION & EXPANSION JOINTS
​
​
Challenges in Steam Piping Design
Challenges in High-Pressure Piping Systems
Designing and maintaining high-pressure piping systems presents numerous challenges due to the complexity, risks, and precision required in their execution. These challenges are particularly evident in industries like oil and gas, power generation, chemical processing, and other heavy industries where high-pressure systems are critical to operations. Here are some of the key challenges faced in high-pressure piping design and management:
-
Material Selection and Durability
High-pressure piping systems are exposed to extreme conditions, including high temperatures, corrosive environments, and mechanical stresses. Selecting the right materials that can withstand these conditions while ensuring longevity and safety is a significant challenge. Materials must not only resist pressure but also be resistant to corrosion, fatigue, and wear over time. -
Pressure Resistance and Safety
One of the biggest concerns in high-pressure systems is ensuring that the piping can safely handle the intended pressure without risk of failure. This requires accurate pressure analysis, including the consideration of pressure surges, vibration, and thermal expansion. The potential risks of a pressure-related failure—such as leaks, explosions, or catastrophic system breakdowns—demand meticulous design and regular maintenance. -
Thermal Expansion and Contraction
High-pressure piping systems are often subjected to temperature fluctuations that lead to thermal expansion and contraction. Managing this expansion is essential to preventing stress and damage to the pipes. Expansion joints, supports, and proper routing must be carefully designed to accommodate these changes while maintaining the integrity of the system. -
Stress Analysis and Fatigue Resistance
Piping systems under high pressure are subjected to significant mechanical stresses, both from the internal fluid pressure and external forces such as wind, seismic activity, and operational vibrations. Stress analysis and fatigue resistance are critical to ensuring the system's structural integrity over its operational life. Improperly designed or maintained systems are vulnerable to stress fractures, which can lead to leaks or failures. -
Regulatory Compliance
High-pressure piping systems are subject to strict industry regulations and safety standards. Compliance with national and international codes, such as ASME, ASNI, and API, is essential to ensure the safety, reliability, and environmental sustainability of the system. Navigating these codes and keeping up with regulatory changes can be a complex and time-consuming task. -
Leakage Prevention
High-pressure systems are highly susceptible to leaks, which can pose serious safety, environmental, and operational risks. Ensuring tight seals, proper welding, and high-quality material selection are essential for preventing leaks. Leak detection systems, monitoring, and regular inspections are also vital components in managing these risks. -
Design Optimization
Achieving a balance between efficiency, cost-effectiveness, and performance is a challenging task. Over-designing systems can lead to unnecessary costs, while under-designing can compromise safety and functionality. Optimizing the layout, material usage, and pipe sizing is key to developing a reliable system without overburdening the budget. -
Installation and Maintenance
The installation and maintenance of high-pressure piping systems require a high level of expertise and precision. Installation errors or poor welding techniques can lead to weak points in the system that may fail under pressure. Additionally, maintaining high-pressure systems involves regular inspections, monitoring for signs of wear or corrosion, and performing timely repairs to avoid system breakdowns. -
Environmental Factors
Environmental considerations, such as corrosive environments, seismic activity, temperature extremes, or the presence of hazardous chemicals, add another layer of complexity to high-pressure piping design. The system must be designed to accommodate these factors, using appropriate protective coatings, reinforcements, and monitoring systems to prevent failure. -
System Integration
High-pressure piping systems must often be integrated with other parts of an industrial infrastructure, including pumps, valves, and reactors. Ensuring smooth integration while maintaining the performance and safety of the entire system is a complex challenge. It requires detailed planning and coordination across multiple disciplines of engineering.

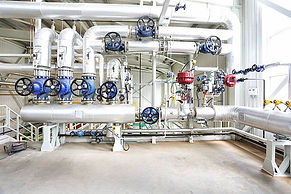

