
DiVYA
PHONE : +91-8374485833,
Mail : storagetanks@mail.com
INDUSTRIAL PIPING DESIGN CONULTANCY SERVICES

Diesel (HSD) Piping System Design Services
Piping Design Consultants- Diesel (HSD) Piping | Divya Engineering
"Divya Engineering offers expert piping design consultancy services specializing in Diesel (HSD) Piping systems. We provide innovative and cost-effective solutions tailored to your project needs
Diesel (HSD) piping refers to the systems used to transport high-speed diesel (HSD) fuel within various infrastructure such as fuel storage tanks, refueling stations, or engines. These piping systems are designed to safely handle the characteristics of diesel fuel, which is flammable and can be hazardous if not properly managed.
Here are the key elements involved in HSD piping systems:
1. Material Selection:
-
Piping Materials: Piping for diesel fuel is typically made of materials that are resistant to corrosion and chemical damage, such as carbon steel, stainless steel, and polyethylene (for smaller systems). The material must be able to withstand the flow of diesel and not degrade over time due to fuel exposure.
-
Fittings and Valves: Valves, elbows, tees, and other fittings are also selected based on their compatibility with diesel fuel. They must be able to seal properly to prevent leakage.
2. Pressure Rating:
-
Diesel piping is often designed to handle certain pressures depending on the application, such as in fuel dispensing systems where high pressure may be required to pump the fuel through hoses. Typically, the pressure ratings for these systems are determined by the maximum working pressure (MWP) of the fuel system.
3. Piping Layout:
-
The layout of the piping system should minimize the risk of leakage and spillage. Proper slope must be provided to ensure drainage of any fuel in case of a leak or system failure.
-
Special attention should be given to grounding and bonding to prevent static discharge and potential sparks in the system.
4. Safety Considerations:
-
Leak Prevention: Diesel fuel piping systems should include safety measures like automatic shut-off valves, leak detection systems, and emergency cut-off switches.
-
Ventilation: Ventilation is essential, particularly in storage tanks, to avoid the accumulation of explosive vapors.
-
Fire Prevention: Fire-resistant materials and fire breaks must be considered for the protection of piping and tanks in case of an emergency.
5. Piping Insulation:
-
Insulation: Insulation is important in colder climates where diesel fuel could gel or thicken. Insulated piping helps maintain the proper flow of fuel.
-
Heating: In certain environments, electrical heating tapes or heat-traced pipes are used to maintain the temperature of the fuel.
6. Regulatory Compliance:
-
Standards and Codes: Piping for diesel fuel must comply with national and international standards, including codes like ASME B31.4 (for liquid pipelines) or NFPA 30 (for flammable liquids).
-
Environmental Considerations: Regulations regarding spill containment and environmental protection must also be followed to avoid fuel contamination and leakage into the environment.
7. Maintenance and Inspection:
-
Regular inspections of diesel piping systems are essential to check for wear, corrosion, or other issues that may affect performance. Maintenance procedures should be in place for checking fuel quality, monitoring for leaks, and ensuring that all components are functioning as intended.
DIESEL (HSD) PIPING DESIGN AND DRAFTING
Diesel (HSD) Piping Design Services
Divya Engineering is a leading consultancy specializing in the design and optimization of Diesel (HSD) piping systems. The company’s expertise is centered around industries where the integrity of fuel transportation systems is paramount, such as oil and gas, petrochemicals, power generation, and industrial applications. Divya Engineering offers a full spectrum of services, from creating detailed CAD drawings and conducting pipe stress analysis to providing 3D modeling and fabrication/erection drawings. The company is committed to ensuring that each design is optimized for both performance and safety, complying with critical industry standards like ASME B31.1 and ASME B31.3. Along with their core offerings, Divya Engineering is also renowned for serving diverse industries by providing innovative solutions in piping layout optimization, stress analysis using CAESAR II, and creating Piping and Instrumentation Diagrams (P&IDs).
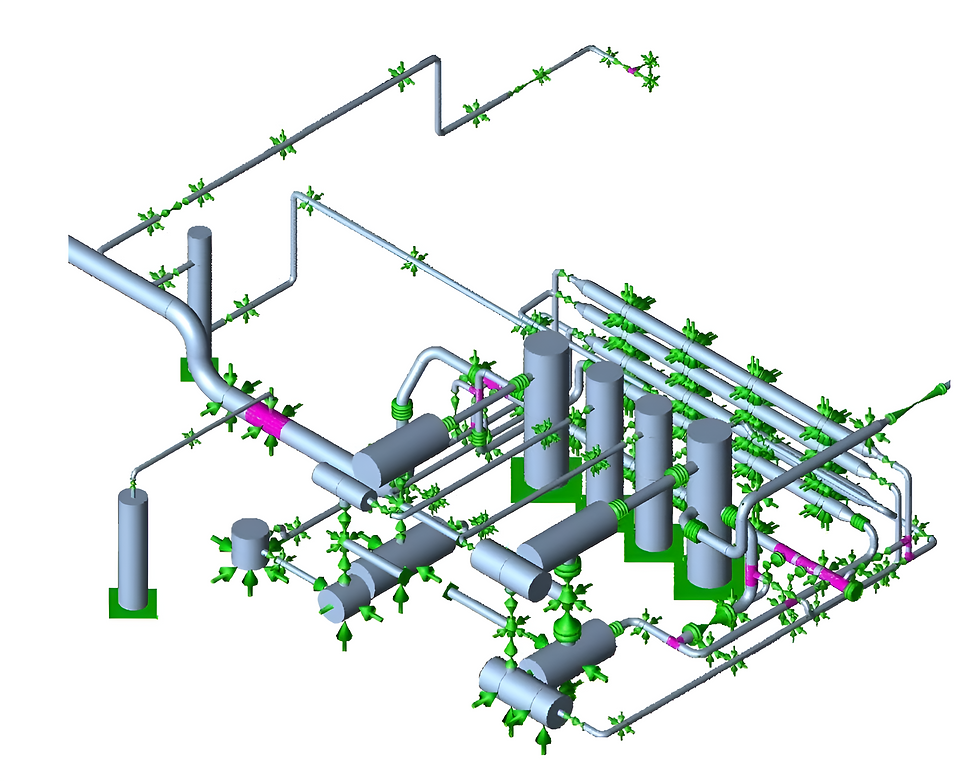
DIESEL (HSD) PIPING LAYOUT AND ROUTING
Diesel (HSD) Piping Design and Engineering Expertise
Divya Engineering’s approach to designing Diesel (HSD) systems incorporates a wide range of specialized services, all of which are essential for creating reliable, efficient, and safe fuel transportation systems. One of the most critical phases in design is Piping Layout and Routing, which ensures that Diesel (HSD) systems are engineered to meet both performance requirements and safety regulations in fuel transportation.
This process is fundamental for both industrial and energy applications, ensuring the effective transport of diesel fuel while optimizing system efficiency, space usage, and access for maintenance. To achieve the best results, Divya Engineering employs cutting-edge tools to model, visualize, and plan piping systems with precision.

DIESEL (HSD) PIPING SUPPORT DESIGN
A key element of Diesel (HSD) piping design is Piping Support Design, which ensures the structural integrity of systems subjected to extreme temperatures, vibrations, and potentially corrosive environments. Divya Engineering’s team specializes in designing robust supports, hangers, and brackets to secure pipes, minimizing the risk of system failure. By using advanced stress analysis tools like CAESAR II and AutoCAD Plant 3D, as well as BIM platforms like Revit, the company ensures the piping system can withstand mechanical stresses.

DIESEL (HSD) PIPING MATERIAL SELECTION
Material Selection for Diesel (HSD) Systems
When designing Diesel (HSD) systems, material selection is critical to ensuring long-term performance. Divya Engineering helps clients choose materials that are durable, resistant to the unique challenges posed by diesel fuels, and suitable for extreme operating conditions. Factors like pressure tolerance, temperature resistance, and corrosion resistance are carefully considered to ensure the longevity and efficiency of the system

DIESEL (HSD) PIPING STRESS ANALYSIS
Piping Stress Analysis and Compliance
Piping Stress Analysis is another essential service, particularly for systems designed to transport Diesel (HSD), which must withstand pressure surges, thermal expansion, and external loads. Divya Engineering conducts thorough analyses to ensure that Diesel (HSD) systems are both durable and safe, using industry-leading software like CAESAR II to simulate and evaluate the stresses placed on piping. Compliance with industry standards is paramount, with Divya Engineering adhering to:
-
ASME B31.3: Governs the design of process piping systems, ensuring systems are robust enough to handle corrosive fluids like Diesel (HSD).
-
ASME B31.1: Covers power piping systems, including those used in systems that transport fuels and other high-temperature, high-pressure liquids.
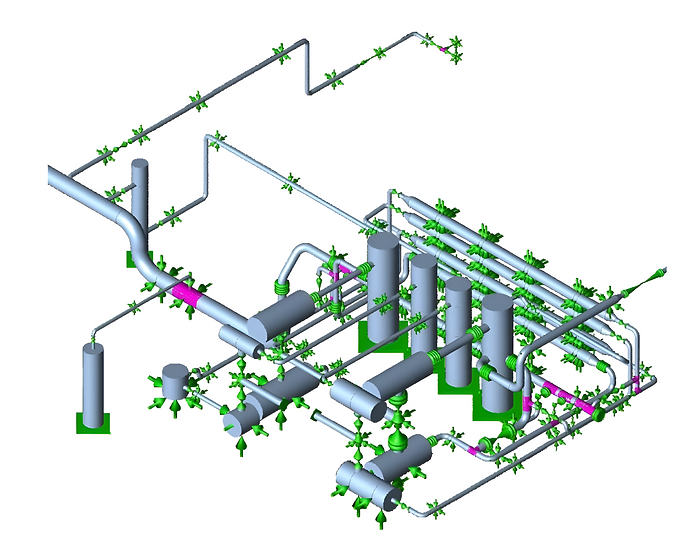
DIESEL (HSD) PIPING AND INSTRUMENTATION DIAGRAMS (P&IDS):
P&IDs and Specification Development
As part of their comprehensive services, Divya Engineering creates Piping and Instrumentation Diagrams (P&IDs) for Diesel (HSD) systems. These diagrams detail the components and layout of the piping system, including valves, pumps, instrumentation, and control systems. P&IDs help simplify system troubleshooting and maintenance while ensuring safe operation. Along with P&IDs, Divya Engineering develops clear piping specifications and standards that outline the necessary parameters for the installation, operation, and maintenance of Diesel (HSD) systems. These specifications guarantee that the system complies with both local and international standards, ensuring reliability and safety.
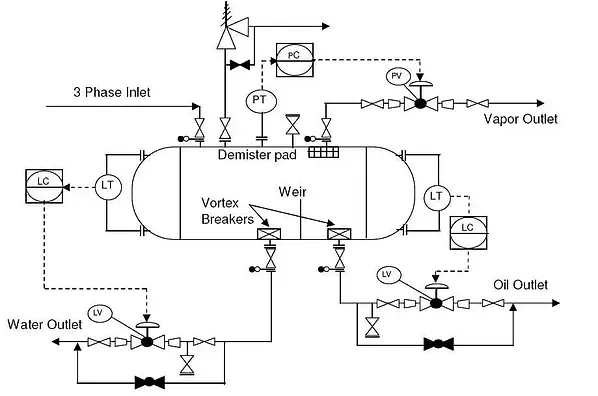
DIESEL (HSD) DEVELOPMENT OF PIPING SPECIFICATIONS AND STANDARDS
The development of piping specifications and standards is another cornerstone of Divya Engineering’s turbine piping design services. These specifications ensure that the turbine piping system is designed, installed, and maintained according to consistent, reliable, and efficient practices. This is particularly important in ensuring the safety, performance, and durability of the system, while ensuring compliance with both local and international regulations.
Divya Engineering adopts a structured, phased methodology when developing these specifications and standards, ensuring comprehensive coverage throughout the project lifecycle. This process is essential for turbine piping design, as it guarantees the correct selection of materials, accurate pipe sizing, and adherence to national and international standards. By providing detailed piping specifications, Divya Engineering ensures that turbine systems operate at peak efficiency

DIESEL (HSD) PIPE SIZING AND HYDRAULIC CALCULATIONS
Advanced Modeling and Hydraulic Calculations
To optimize the efficiency and cost-effectiveness of the Diesel (HSD) system, Divya Engineering employs hydraulic calculations and advanced pipe sizing methods. This ensures the system performs at peak efficiency while reducing operational costs.
With the use of 3D modeling technology, Divya Engineering provides highly accurate visual representations of the entire piping system, which allows for better planning, reduced errors, and more reliable construction outcomes. This 3D approach minimizes the risk of rework and ensures a smoother transition from design to construction
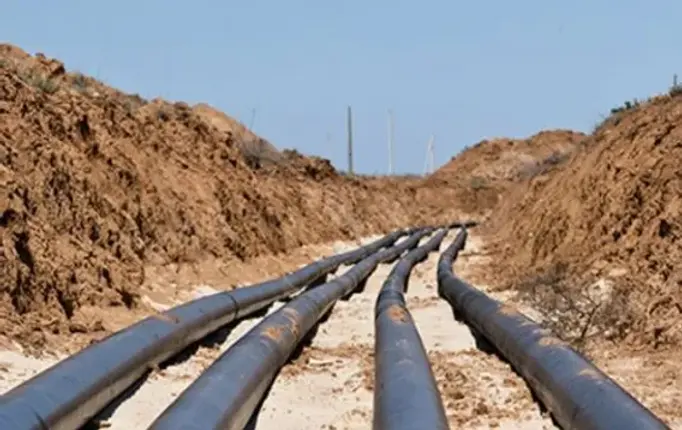
DIESEL (HSD) 3D MODELING AND DESIGN
With the use of 3D modeling technology, Divya Engineering provides highly accurate visual representations of the entire piping system, which allows for better planning, reduced errors, and more reliable construction outcomes. This 3D approach minimizes the risk of rework and ensures a smoother transition from design to construction.

DIESEL (HSD) ISOMETRIC/FABRICATION/ERECTION DRAWINGS
Isometric, Fabrication, and Erection Drawings
Once the design phase is complete, Divya Engineering produces a detailed set of Isometric Drawings, Fabrication Drawings, and Erection Drawings. These drawings are crucial for the precise construction and installation of the Diesel (HSD) system, ensuring each component is correctly fabricated, assembled, and installed. Isometric drawings provide a 3D perspective of the entire system, while fabrication drawings offer detailed information on individual components and materials. Erection drawings guide the on-site assembly process, ensuring that the final installation aligns with the design specifications.
By providing these comprehensive services, Divya Engineering ensures the successful design, implementation, and operation of Diesel (HSD) piping systems that are not only safe and reliable but also efficient and durable in demanding industrial environments. Their commitment to quality, innovation, and compliance guarantees the highest standards for fuel transportation.
Diesel(HSD) Piping Design Services
Piping Design Consultants- Diesel(HSD) Piping | Divya Engineering
Piping Design and Drafting: Creating detailed CAD drawings and design calculations forDiesel(HSD) piping systems used in power plants, refineries, and other industrial facilities.
​
Pipe Stress Analysis: Performing static and dynamic stress analysis using software like CAESAR II to ensure the Diesel(HSD) piping system can withstand operational and environmental stresses.
​
3D Modeling and Design: Using software such as PDS, PDMS, or Auto Plant to create 3D models of Diesel(HSD) piping systems for better visualization and accuracy.
​
Isometric/Fabrication/Erection Drawings: Preparing detailed drawings for the fabrication and installation of Diesel(HSD) piping systems.
​
Support Detail Drawing Preparation: Designing and detailing the necessary supports for the Diesel(HSD) piping system to ensure stability and safety.
​
Project Management: Managing the entire Diesel(HSD) piping design project from initial conceptualization through fabrication and commissioning.
​
Compliance with Standards: Ensuring that the design complies with relevant standards such as ASME B31.1 for power piping and ASME B31.3 for process piping.
​
BILL OF MATERIAL, INSULATION & EXPANSION JOINTS
​
​
Challenges Diesel(HSD) Piping System design
​
Designing Diesel (HSD) Piping Systems comes with several unique challenges due to the nature of the fuel, operational conditions, and safety requirements. Below are the key challenges encountered in the design process of Diesel (HSD) piping systems:
1. Material Selection and Corrosion Resistance:
Diesel is a relatively aggressive fuel, and the piping system must be designed using materials that resist corrosion and degradation over time. Factors such as moisture content in the diesel, chemical additives, and exposure to various environmental conditions can lead to corrosion and rust, which compromises the integrity of the system. Choosing corrosion-resistant materials like stainless steel, carbon steel with protective coatings, or composite materials is critical to ensure long-term durability.
2. Pressure and Flow Control:
Diesel (HSD) systems must operate under specific pressure and flow conditions to ensure consistent fuel delivery. Fluctuations in pressure or improper flow rates can lead to system inefficiencies, fuel wastage, or even damage to equipment. Designing the system to maintain optimal pressure and flow requires careful planning of pump specifications, valve placement, and system layout.
3. Leak Prevention and Detection:
Leaks in a Diesel (HSD) piping system can have severe consequences, including environmental contamination, fire hazards, and operational downtime. Ensuring leak-free joints and connections is a challenge, particularly in a system that may undergo temperature and pressure fluctuations. The design must include reliable sealing solutions, leak detection sensors, and emergency shut-off systems to promptly address any leaks.
4. Fire and Explosion Risk Mitigation:
Diesel is flammable, and any leakage or malfunction could result in fire or explosion risks. In addition to material selection, the piping system must incorporate features like fire-resistant materials, grounding and bonding of equipment to prevent static discharge, flame arrestors, and explosion-proof valves. The system design must comply with industry safety standards, such as NFPA, to minimize fire hazards.
5. Temperature Variations:
Diesel (HSD) piping systems are often exposed to varying environmental temperatures, which can cause expansion and contraction of the pipes. In extreme cases, this could result in stress and eventual failure. The system must be designed with adequate expansion joints, flexible connectors, and temperature compensation mechanisms to handle thermal expansion and contraction without causing damage to the piping.
6. Environmental Protection:
Diesel fuel leaks or spills can have serious environmental impacts, especially in sensitive areas like marine environments or near water sources. The piping design must include containment measures such as secondary containment systems, leak-proof seals, and appropriate drainage systems. Designers must also ensure compliance with environmental regulations to minimize the risk of spills and reduce the environmental footprint of the system.
7. Accessibility for Maintenance and Inspection:
Diesel piping systems need to be regularly inspected and maintained to ensure optimal performance and safety. Designing a system with sufficient access points for routine inspection and maintenance is essential, particularly in areas that may be difficult to reach. The layout of the piping system must allow for easy inspection, cleaning, and repairs without disrupting operations.
8. System Integration:
Diesel (HSD) piping systems are often integrated with other systems such as fuel tanks, filtration units, pumps, and other infrastructure. Ensuring seamless integration while avoiding conflicts with other systems or structures can be challenging. Designers must account for the spatial constraints of existing facilities and ensure compatibility with other equipment.
9. Compliance with Standards and Regulations:
Diesel (HSD) piping systems are subject to numerous regulations and standards, including those from organizations such as the American Petroleum Institute (API), ASTM, NFPA, and local environmental agencies. Compliance with these regulations is crucial, not only to ensure safety but also to avoid legal issues and penalties. Meeting these regulatory requirements while balancing cost and performance adds complexity to the design process.
10. Vibration and Mechanical Stress:
The pumps and equipment used in Diesel (HSD) systems can create vibrations that are transmitted through the piping. These vibrations can lead to wear and tear, loosening of joints, or even cracks in the pipes over time. The system must be designed with vibration isolation measures, such as flexible couplings, dampeners, and proper pipe supports to reduce the impact of mechanical stress.
11. Fuel Quality and Contamination Prevention:
The design of the piping system must take into account the potential for fuel contamination, whether through water, dirt, or microbial growth. Proper filtration and separation systems must be integrated to ensure that only clean fuel is delivered. The piping system design should also prevent the accumulation of sediments or water at low points to maintain fuel quality.
12. Cost Considerations:
The design and installation of Diesel (HSD) piping systems can be costly, especially when considering the need for high-quality materials, advanced safety features, and compliance with regulations. Balancing cost-efficiency with safety and durability requires careful selection of materials and design features that optimize both performance and long-term maintenance costs.
Addressing these challenges requires a deep understanding of fuel handling systems, material science, and safety protocols. With the right design and engineering expertise, these challenges can be overcome, leading to the creation of safe, reliable, and efficient Diesel (HSD) piping systems that meet both operational needs and regulatory requirements.


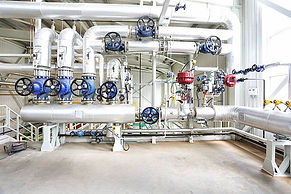
