
DiVYA
PHONE : +91-8374485833,
Mail : storagetanks@mail.com
INDUSTRIAL PIPING DESIGN CONULTANCY SERVICES

Cryogenic Piping Design Services
Piping Design Consultants- Cryogenic Piping | Divya Engineering
​
Cryogenic piping refers to a system of pipes used to transport fluids at extremely low temperatures, typically below -150°C (-238°F). These fluids are often gases like liquefied natural gas (LNG), liquid oxygen (LOX), liquid nitrogen (LN2), liquid hydrogen (LH2), and helium, which are stored or transported in their liquid state under high pressure.
Due to the extremely low temperatures, cryogenic piping systems need to be carefully designed and constructed to maintain the integrity of both the piping and the materials being transported. Here's an overview of key considerations:
Key Features of Cryogenic Piping Systems:
-
Materials:
-
Metals: The most common materials used for cryogenic piping are stainless steel and carbon steel. Stainless steel, especially 304 and 316 grades, is often preferred for its resistance to corrosion and ability to maintain strength at low temperatures.
-
Insulation: Cryogenic pipes are typically insulated to prevent heat from entering the system and causing the cryogenic liquid to vaporize. Common insulation materials include expanded polystyrene, vacuum-insulated pipes, and fiberglass.
-
-
Thermal Expansion:
-
Materials used for cryogenic piping must be chosen to handle the thermal expansion that occurs when the fluid temperature rises and contracts. Cryogenic pipes often have flexible joints or expansion loops to accommodate this movement.
-
-
Pressure and Flow Control:
-
Cryogenic piping systems are often under high pressure due to the compression of the liquid form of gases. The pressure relief valves, pumps, and regulators need to be specifically designed to function safely at cryogenic temperatures.
-
-
Sealing:
-
The seals used in cryogenic piping must be made from materials that perform well at low temperatures, such as PTFE (polytetrafluoroethylene), graphite, or specially formulated elastomers.
-
-
Condensation and Boil-off:
-
Any heat ingress into the system can lead to the boil-off of the cryogenic liquid, which may result in the generation of gas. This can be particularly problematic for systems like LNG pipelines. Therefore, vapor recovery systems or refrigeration units may be employed to prevent excessive vaporization.
-
-
Safety:
-
Cryogenic fluids can be hazardous because they are extremely cold and can cause frostbite or severe thermal burns on contact. Adequate ventilation, safety systems, and emergency shutdown valves are essential to protect personnel working with cryogenic fluids.
-
-
Flow Control Devices:
-
The valves and flow control devices used in cryogenic systems need to be able to operate at low temperatures without becoming brittle or malfunctioning. Specially designed cryogenic valves are used, often with extended bonnets to protect the valve stem from freezing.
-
Applications of Cryogenic Piping:
-
Natural Gas Industry: Cryogenic piping is commonly used in LNG (Liquefied Natural Gas) terminals and pipelines to transport gas in its liquid form.
-
Medical and Industrial Gases: Systems for liquid oxygen and liquid nitrogen delivery, typically used in hospitals, laboratories, and various industrial applications.
-
Space Exploration: Cryogenic fluids like liquid hydrogen and liquid oxygen are used as fuel for rockets, which require specialized cryogenic pipelines.
-
Food & Beverage Industry: Cryogenic liquids are used in freezing and refrigeration applications.
Design Considerations:
-
Thermal Management: Preventing heat from entering the system is crucial. Cryogenic pipes are usually insulated with materials that minimize heat transfer.
-
Flexibility: Since materials can become brittle at low temperatures, cryogenic pipes need to account for movement and thermal stresses with appropriate joints or flexible segments.
-
Leakage Prevention: Cryogenic systems are highly sensitive to leakage, which could lead to hazardous conditions. Welded joints are often used in place of threaded connections to reduce the risk of leaks.
Common Standards:
-
ASME B31.3: A common standard for the design of piping systems in the chemical and petrochemical industries, including cryogenic applications.
-
ASME B31.9: Specifically covers the design of piping systems in industrial applications, including cryogenic piping.
-
ISO 9001: Often applied to the quality management systems of companies producing cryogenic equipment.
CRYOGENIC PIPING DESIGN AND DRAFTING
Divya Engineering is a consultancy dedicated to providing expert design services for cryogenic piping systems. Their extensive offerings encompass creating detailed CAD drawings, conducting design calculations, performing pipe stress analysis, and developing 3D models, along with fabrication and erection drawings. The team focuses on critical aspects as material selection, support detail design, and project management while ensuring adherence to important standards like ASME B31.1 andME B31.3. In addition to cryogenic systems, Divya Engineering caters to a of industries, including oil and gas, petrochemicals, and power generation, offering services that include piping layout optimization, support design, stress analysis with CAESAR II, and the creation of Piping and Instrument Diagrams (P&IDs), among others.
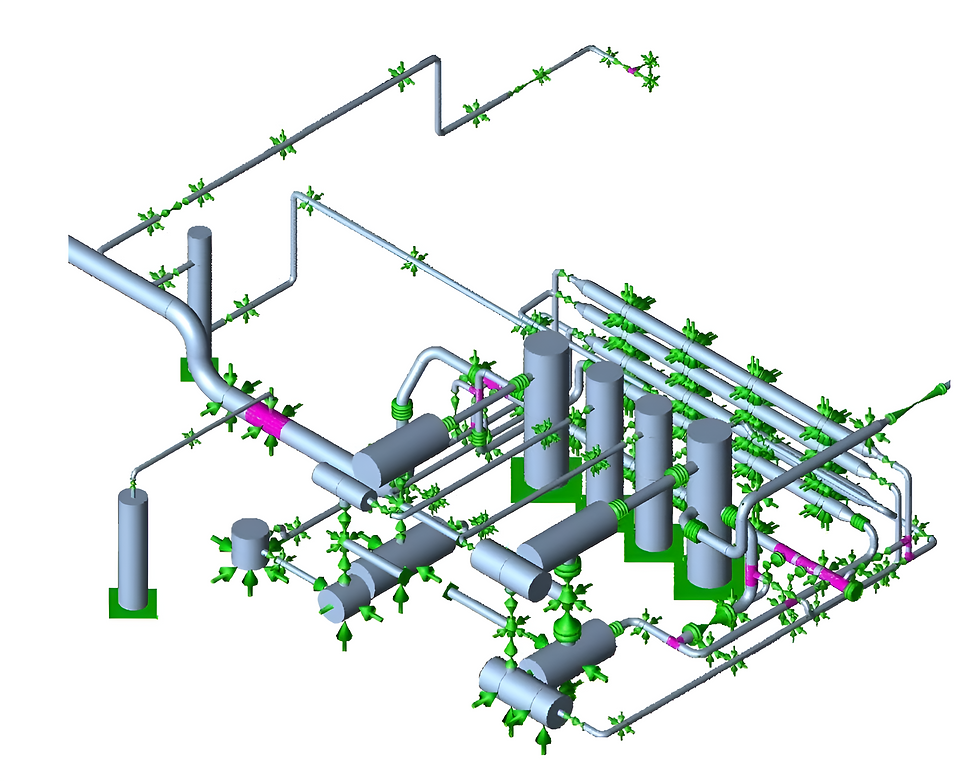
CRYOGENIC PIPING LAYOUT AND ROUTING
Divya Engineering's Cryogenic Piping Design Services encompass a range of essential offerings, including Piping Layout and Routing. This service is crucial for the effective design of cryogenic distribution systems across residential, commercial, and industrial applications. It guarantees the safe and efficient transportation of cryogenic fluids through the piping network while addressing space limitations, optimizing system performance, and facilitating maintenance. ** Tools Used for Piping Layout and Routing** · AutoCAD: Utilized for both 2D and 3D design, AutoCAD is commonly employed to create detailed cryogenic piping layouts and routing plans. · Revit: This software is ideal for Building Information Modeling (BIM), particularly for intricate cryogenic piping systems within structures. · Plant 3D: Designed for industrial cryogenic systems, Plant 3D assists in modeling, routing, and optimizing piping configurations. · CAESAR II: Used for stress analysis and design validation, CAESAR II ensures the piping system can withstand operational requirements.

CRYOGENIC PIPING SUPPORT DESIGN
Divya Engineering's Cryogenic Piping Design Services encompass a range of essential components, including Piping Support Design. This critical aspect of any piping system, particularly within cryogenic distribution frameworks, ensures structural integrity, operational efficiency, and safety throughout the system's lifespan. The service focuses on creating robust supports, hangers, and brackets that secure the pipes, protecting them from potential damage caused by movement, vibration, thermal expansion, and other external forces. To achieve this, advanced software tools such as CAAR II, which is instrumental for piping stress analysis and support design, AutoCAD Plant 3D for 3D modeling layout integration, and Revit for precise 3D visualization in integrated designs, are utilized.

CRYOGENIC PIPING MATERIAL SELECTION
Piping Material Selection is a critical aspect of cryogenic piping design, and Divya Engineering's services likely include assisting clients choosing the most suitable materials for their cryogenic distribution systems. Proper material selection guarantees that system is durable, effective, and capable of withstanding the pressures, temperatures, and other conditions will encounter throughout its lifecycle. Typically, Piping Material Selection encompasses evaluating factors such as pressure, temperature, resistance, and cost efficiency. Whether for residential, commercial, or industrial applications, selecting the right materials ensures optimal performance and long-term sustainability. If you’d like to discuss specific for your projects, feel free to reach out.

CRYOGENIC PIPING STRESS ANALYSIS
piping Stress Analysis is a crucial component of Divya Engineering's CRYOGENIC piping design services. This analysis ensures that the system is structurally robust and capable of withstanding the operational stresses it will face throughout its lifespan. In CRYOGENIC systems, stress analysis plays a vital role in identifying potential challenges such as thermal expansion, pressure surges, vibrations, and mechanical loads, which could result in failures, leaks, or degradation of the system. **Industry Standards and Codes for Piping Stress Analysis** Divya Engineering adheres industry standards during their piping stress analysis, including: - **ASME31.3:** This standard pertains to process piping systems, outlining the necessary design, materials, and considerations for CRYOGENIC and industrial piping systems. - **ASME B31.1:** This code addresses power piping, encompassing steam, CRYOGENIC, and other fluid systems under. Piping Stress Analysis is an indispensable service provided by Divya Engineering.

CRYOGENIC PIPING AND INSTRUMENTATION DIAGRAMS (P&IDS):
Divay Engineering Cryogenic Piping Design Services - Piping and Instrumentation Diagrams (P&IDs): Piping and Instrumentation Diagrams (P&IDs) are crucial tools in design, operation, and maintenance of cryogenic piping systems. Divay Engineering's Cryogenic Piping Design Services encompass the creation of P&IDs that ensure clarity in system design, operation, and future troubleshooting. What are P&IDs? A Piping and Instrumentation Diagram (P&ID) is a detailed graphical representation of piping system that illustrates the relationships between pipes, equipment, valves, instruments, and control systems. It depicts the flow of fluids through the piping system and includes major components as pumps, filters, tanks, and any associated instrumentation or control devices.

CRYOGENIC DEVELOPMENT OF PIPING SPECIFICATIONS AND STANDARDS
When it comes to CRYOGENIC piping systems, the development of piping specifications and standards is a fundamental service offered by Divya. These specifications and standards ensure that the entire piping system is designed, installed, and maintained according to consistent, reliable and efficient practices. They help guarantee system safety, performance, longevity, and compliance with local and international standards. Divya Engineering employs a systematic and phased approach in developing piping specifications and standards to ensure comprehensive coverage and project success. In summary, the creation of these is a critical service that Divya Engineering provides for CRYOGENIC piping design, ensuring proper material, accurate pipe sizing, and adherence to local regulations.
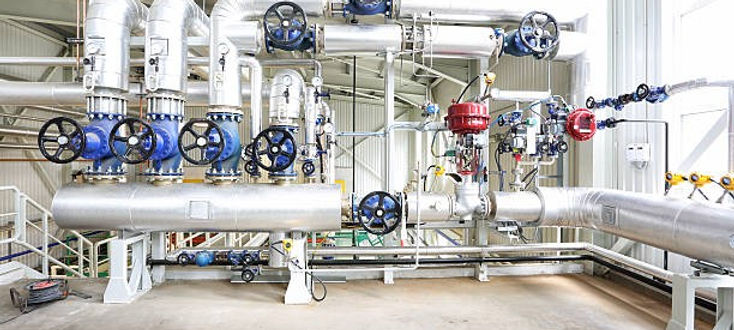
CRYOGENIC PIPE SIZING AND HYDRAULIC CALCULATIONS
ya Engineering's CRYOGENIC piping design services encompass critical elements such as pipe sizing and hydraulic calculations, which are vital for ensuring the efficiency, reliability and longevity of the system. Proper pipe sizing and hydraulic analysis are essential to optimizing the performance of CRYOGEN systems across industrial, commercial, and municipal applications. At Divya Engineering, we adopt a systematic and detailed approach to pipe sizing and hydraulic calculations, carefully considering all parameters to achieve optimal system performance. By accurate calculations, we can enhance flow efficiency, minimize pressure losses, and select the most suitable materials for CRYOGENIC applications.
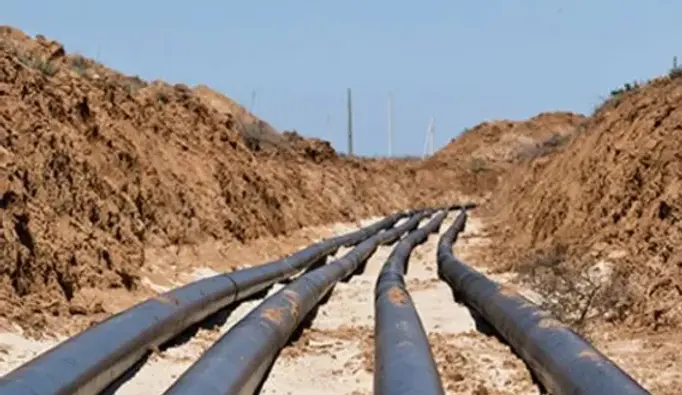
CRYOGENIC 3D MODELING AND DESIGN
In the field of CRYOGENIC piping design, 3D modeling design are essential for creating efficient, precise, and visually clear representations of piping systems. Divya Engineering offers advanced 3D modeling and design services to ensure that CRYOGENIC piping systems are meticulously designed, optimized, and executed flawlessly without the risk of errors or rework. 3D modeling and design play a pivotal role in modern CRYOGENIC piping system design, allowing Divya Engineering to enhance the design process, minimize errors, and guarantee that the system is efficient, cost-effective, and easy to implement. The capability to visualize, simulate, and analyze the entire system before construction enables the identification of potential challenges and the development of a design that performs optimally under real-world conditions. If you're in need of a comprehensive and robust 3D design for your CYOGENIC piping system, Divya Engineering possesses the tools and expertise to deliver exceptional results.

CRYOGENIC ISOMETRIC/FABRICATION/ERECTION DRAWINGS
At Divya Engineering, the creation of isometric, fabrication, and erection drawings is a crucial part of the cryogenic piping design process. These drawings are essential for the successful installation and operation of the cryogenic system. They provide clear, accurate, and detailed instructions for the construction team, ensuring that system is built according to the design specifications and industry standards. 1. What are Isometric, Fabrication, and Erection Drawings? Isometric Drawings: An isometric drawing is a type of 3D representation of the piping system, drawn at an angle of 30 degrees to the horizontal. It visually conveys the layout and orientation of pipes, valves, and other system components. Purpose: Isometric drawings are vital for presenting complex pipe layouts in an easy-tostand format, allowing viewers to visualize the system in three dimensions.
Cryogenic Piping Design Services
Piping Design Consultants- Cryogenic Piping | Divya Engineering
Piping Design and Drafting: Creating detailed CAD drawings and design calculations for Cryogenic piping systems used in power plants, refineries, and other industrial facilities.
​
Pipe Stress Analysis: Performing static and dynamic stress analysis using software like CAESAR II to ensure the Cryogenic piping system can withstand operational and environmental stresses.
​
3D Modeling and Design: Using software such as PDS, PDMS, or Auto Plant to create 3D models of Cryogenic piping systems for better visualization and accuracy.
​
Isometric/Fabrication/Erection Drawings: Preparing detailed drawings for the fabrication and installation of Cryogenic piping systems.
​
Support Detail Drawing Preparation: Designing and detailing the necessary supports for the Cryogenic piping system to ensure stability and safety.
​
Project Management: Managing the entire Cryogenic piping design project from initial conceptualization through fabrication and commissioning.
​
Compliance with Standards: Ensuring that the design complies with relevant standards such as ASME B31.1 for power piping and ASME B31.3 for process piping.
​
BILL OF MATERIAL, INSULATION & EXPANSION JOINTS
​
​
Challenges in Cryogenic Piping Design
Designing cryogenic piping systems presents several unique and complex challenges due to the extreme conditions associated with low temperatures. These systems must handle liquids and gases at temperatures that can be as low as -150°C (-238°F) or lower, which introduces a range of design considerations that need to be addressed to ensure safety, performance, and longevity. Some of the key challenges in cryogenic piping design include:
1. Material Selection
One of the primary challenges in cryogenic piping design is selecting the appropriate materials that can withstand extremely low temperatures without becoming brittle or losing strength. At cryogenic temperatures, many materials can experience reduced toughness, leading to the risk of cracking or failure. The designer must carefully choose materials with excellent low-temperature properties, such as stainless steel alloys, carbon steel, or specialized cryogenic-resistant materials. Additionally, materials must be compatible with the specific cryogenic fluid (such as liquid nitrogen, oxygen, or LNG) to prevent corrosion or degradation.
2. Thermal Insulation
Cryogenic fluids need to be kept at low temperatures, which requires effective thermal insulation to minimize heat gain from the environment. Poor insulation can result in vaporization or temperature fluctuations that affect the system’s efficiency and safety. Designing a reliable thermal insulation system to minimize heat transfer while preventing condensation and frost formation around the piping is crucial. The insulation materials must also be able to withstand low temperatures without degrading over time.
3. Thermal Expansion and Contraction
Materials used in cryogenic piping systems expand and contract due to temperature variations. As the system undergoes dramatic cooling, the pipes shrink, and when the fluid warms up, the pipes expand. These fluctuations can cause mechanical stress and potential damage if not properly accounted for. Proper expansion joints, flexible piping, or other mechanisms must be incorporated into the design to accommodate these movements and avoid pipe failure or system malfunctions.
4. Pressure Control and Safety
Cryogenic fluids are typically stored or transported at very high pressures, and any fluctuation in pressure can lead to system instability or even catastrophic failure. The design must ensure that the piping system is capable of withstanding these pressures while maintaining safety under extreme conditions. Additionally, pressure relief valves, rupture disks, and other safety devices must be incorporated into the design to prevent over-pressurization and ensure the safety of both the system and the personnel operating it.
5. Vibration and Mechanical Stress
Cryogenic pipes can be subject to vibration caused by fluid flow, pressure surges, or external forces. Vibration, when not properly managed, can lead to fatigue, joint failure, or the loosening of fasteners. Cryogenic piping systems must be designed to minimize the effects of vibration by incorporating adequate supports, anchors, and vibration-damping solutions to ensure structural integrity and prevent damage to the piping system.
6. Cryogenic Fluid Compatibility
The cryogenic fluid flowing through the piping system can be highly reactive and may require special considerations. For example, oxygen is highly reactive with certain materials, while LNG or liquid nitrogen can cause embrittlement in certain metals. Ensuring compatibility between the piping material and the cryogenic fluid is essential to avoid chemical reactions, material degradation, or corrosion. The design must ensure that valves, pumps, and fittings used in the system are also suitable for cryogenic service.
7. Leak Prevention and Integrity
Cryogenic piping systems must maintain an airtight seal to prevent the loss of cryogenic fluids, which are expensive and hazardous. Any leaks, no matter how small, can lead to significant operational issues, safety hazards, or loss of product. Designing leak-tight systems that account for the behavior of materials under extreme cold, the thermal expansion of joints, and the proper sealing mechanisms is essential.
8. Safety Concerns
Handling cryogenic fluids introduces significant safety concerns, particularly the risk of frostbite, asphyxiation from oxygen deficiency, and explosion hazards due to the volatility of certain cryogenic gases. Piping designs must prioritize safety by incorporating emergency shut-off systems, pressure relief mechanisms, proper venting, and easy access for maintenance. Furthermore, the design must ensure that the piping system minimizes risks associated with accidental spills or failures.
9. Cryogenic Piping System Testing
Given the inherent risks associated with cryogenic systems, thorough testing is critical to ensure the reliability and safety of the design. Challenges include performing pressure tests, leak tests, and cold thermal cycling tests under extreme low temperatures to simulate real-world conditions. These tests must be conducted with precision to ensure that the system can handle the intended operational conditions without failure.
10. Maintenance and Inspection
Due to the harsh conditions, maintenance and inspection of cryogenic piping systems can be challenging. The piping materials may degrade over time, insulation may wear out, and seals can deteriorate. Designing systems that facilitate easy inspection, repair, and maintenance while ensuring that the system remains safe and functional is a critical part of the overall design process.
Conclusion
Cryogenic piping design presents several unique and demanding challenges. From material selection and insulation to pressure management and leak prevention, each aspect of the design must be carefully considered to ensure that the system operates safely and efficiently under extreme temperatures. By addressing these challenges with precise engineering and innovative solutions, cryogenic piping systems can be optimized for long-term reliability, performance, and safety in applications such as liquefied natural gas (LNG) transport, industrial gas storage, and medical oxygen systems.
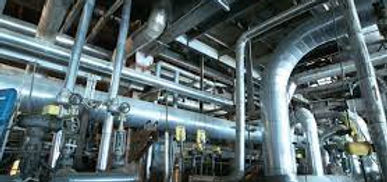

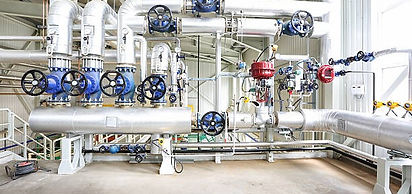
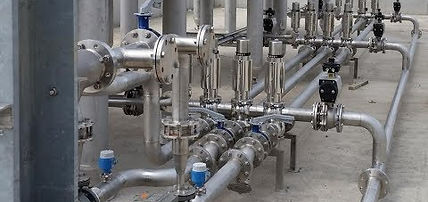