
DiVYA
PHONE : +91-8374485833,
Mail : storagetanks@mail.com
INDUSTRIAL PIPING DESIGN CONULTANCY SERVICES

Ammonia Piping System Design Services
Piping Design Consultants- Ammonia Piping | Divya Engineering
"Divya Engineering offers expert piping design consultancy services specializing in ammonia Piping systems. We provide innovative and cost-effective solutions tailored to your project needs
An ammonia piping system is typically used in industrial refrigeration systems, especially in food processing plants, cold storage facilities, and chemical industries. Ammonia (NH₃) is a highly effective refrigerant due to its thermodynamic properties and relatively low cost. However, due to ammonia's toxicity and flammability, the design, installation, and maintenance of ammonia piping systems must adhere to strict safety standards.
Key Components of an Ammonia Piping System:
-
Pipes: These are the primary carriers for ammonia throughout the system. Materials typically used are:
-
Steel (carbon steel, stainless steel): These materials are strong and durable, and they are used for the majority of ammonia piping.
-
Copper (occasionally): Used in specific circumstances, but not commonly in large industrial systems.
-
-
Valves: Various types of valves are used to control the flow of ammonia:
-
Ball valves
-
Globe valves
-
Check valves
-
Pressure relief valves (to protect the system from overpressure)
-
-
Compressors: These are used to compress ammonia gas in refrigeration systems.
-
Heat Exchangers: Used for heat transfer from the refrigerant (ammonia) to the surrounding environment or a secondary fluid.
-
Evaporators and Condensers: These devices facilitate the transfer of heat from the ammonia to other parts of the system (evaporators for cooling, condensers for rejecting heat).
-
Safety Equipment:
-
Pressure Relief Valves: To ensure the system does not exceed safe pressure levels.
-
Vapor Recovery Systems: For capturing and safely recovering ammonia vapors.
-
Leak Detection Systems: To detect ammonia leaks early and trigger alarms.
-
-
Insulation: Piping systems are often insulated to prevent heat gain or loss, depending on the temperature and function of the pipes.
Design Considerations:
-
System Pressure: Ammonia systems are usually high-pressure systems. Designers need to ensure that the piping, valves, and other components are rated for the correct pressures.
-
Temperature: Ammonia's temperature can range from sub-zero temperatures in the evaporators to high temperatures in the compressors. Material selection needs to account for this thermal stress.
-
Leak Detection: Ammonia is a toxic and hazardous gas. Proper leak detection and alarms are essential. Sensors are often placed at various points in the system, especially near joints and connections.
-
Code Compliance: Depending on the jurisdiction, ammonia systems need to comply with regulations like:
-
ASME (American Society of Mechanical Engineers) Boiler and Pressure Vessel Code
-
ANSI (American National Standards Institute) Standards
-
NFPA (National Fire Protection Association) 59A for ammonia refrigeration systems
-
OSHA (Occupational Safety and Health Administration) standards
-
Safety Considerations:
-
Ventilation: Ammonia systems must be installed in well-ventilated areas to prevent the accumulation of ammonia gas in case of a leak.
-
Ammonia Detection: Early detection of leaks is vital. This can be achieved through ammonia gas detectors or using sensitive odor detectors.
-
Personal Protective Equipment (PPE): Workers in ammonia plants should wear appropriate PPE, including:
-
Gas masks with ammonia cartridges
-
Protective gloves and goggles
-
Full-body suits (for particularly hazardous tasks)
-
Ammonia Piping System Flow Diagram (Simplified Overview):
-
Compressor: Compresses the ammonia gas.
-
Condenser: Cools the ammonia, causing it to condense into a high-pressure liquid.
-
Expansion Valve: Reduces the pressure of the liquid ammonia, causing it to evaporate and absorb heat from the surroundings.
-
Evaporator: Ammonia absorbs heat as it evaporates and chills the surrounding environment.
-
Return to Compressor: The ammonia vapor returns to the compressor, completing the cycle.
AMMONIA PIPING DESIGN AND DRAFTING
Ammonia Piping Design Services
Divya Engineering is a renowned consultancy specializing in the design and optimization of ammonia piping systems. With a strong focus on industries where the safety, reliability, and efficiency of transportation systems are paramount, such as chemicals, petrochemicals, power generation, and industrial applications, Divya Engineering offers an extensive range of services. These include detailed CAD drawings, pipe stress analysis, 3D modeling, and the creation of fabrication and erection drawings. The company is dedicated to ensuring that every design maximizes both performance and safety, in line with strict industry standards like ASME B31.1 and ASME B31.3. Divya Engineering is also known for delivering innovative solutions in piping layout optimization, stress analysis using CAESAR II, and the development of Piping and Instrumentation Diagrams (P&IDs) for a diverse range of industries.
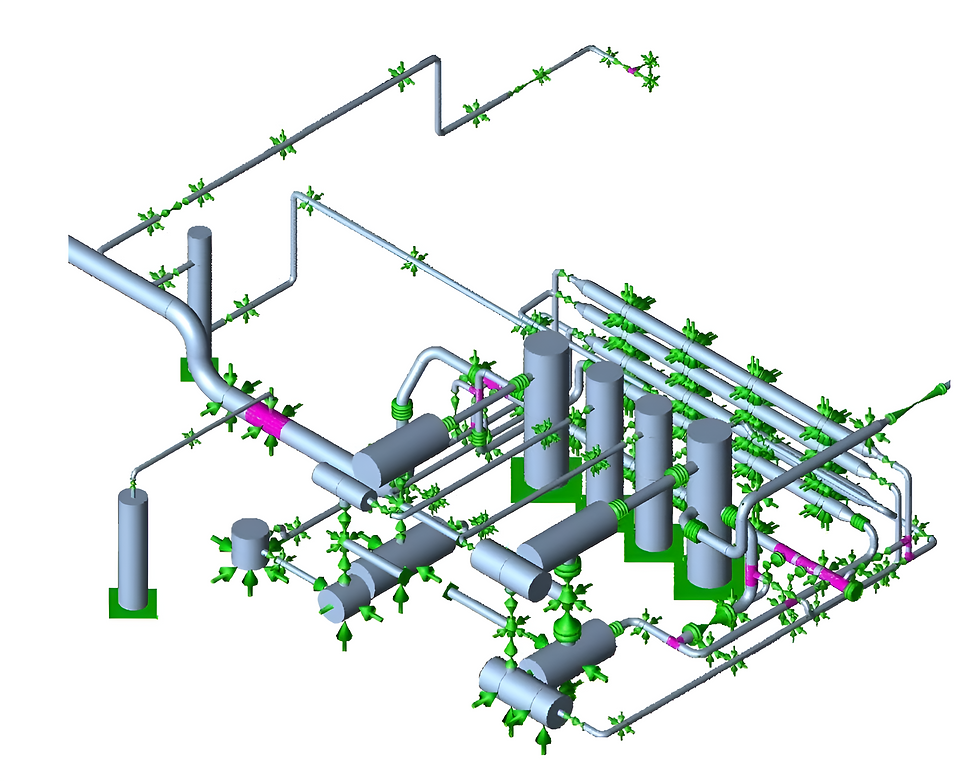
AMMONIA PIPING LAYOUT AND ROUTING
Ammonia Piping Design and Engineering Expertise
Divya Engineering’s approach to ammonia system design covers a broad spectrum of specialized services necessary for creating safe, efficient, and reliable transportation systems. A critical aspect of the design process is the Piping Layout and Routing phase, ensuring that ammonia systems are engineered to meet both operational performance standards and stringent safety requirements. Effective layout planning is particularly crucial for sectors such as industrial manufacturing and energy, where it is essential to guarantee the safe and efficient transport of ammonia, optimize system designs, and make maintenance easier.
To ensure optimal results, Divya Engineering uses cutting-edge tools that model, visualize, and precisely plan ammonia piping systems for maximum accuracy.

AMMONIA PIPING SUPPORT DESIGN
Piping Support Design
A key element in ammonia piping design is Piping Support Design, which focuses on ensuring the structural integrity of systems exposed to high temperatures, mechanical stresses, vibrations, and potentially corrosive conditions. Divya Engineering’s expertise lies in designing durable supports, hangers, and brackets that secure the piping systems, minimizing the risk of failure. By utilizing advanced stress analysis tools like CAESAR II and AutoCAD Plant 3D, as well as BIM technologies like Revit, the company ensures that ammonia piping systems are robust and resilient in challenging environments.

AMMONIA PIPING MATERIAL SELECTION
Material Selection for Ammonia Systems
Material selection plays a critical role in ammonia system design to ensure long-term performance. Divya Engineering collaborates closely with clients to select materials that are highly durable, resistant to the specific challenges posed by ammonia, and capable of withstanding extreme operating conditions. Factors such as pressure tolerance, temperature resistance, and corrosion resistance are thoroughly evaluated to ensure the system's longevity and operational efficiency.

AMMONIA PIPING STRESS ANALYSIS
Piping Stress Analysis and Compliance
Piping stress analysis is vital for systems designed to transport ammonia, as they must withstand pressure surges, thermal expansion, and external loads. Divya Engineering performs thorough stress evaluations to ensure ammonia piping systems are durable and safe, using advanced software like CAESAR II to simulate and analyze the stresses on piping systems. Compliance with industry standards is a top priority for Divya Engineering, and they strictly adhere to the following guidelines:
• ASME B31.3: Governs the design of process piping systems, ensuring systems can effectively handle fluids like ammonia.
• ASME B31.1: Applies to power piping systems, including those used to transport high-pressure and high-temperature fluids such as ammonia

AMMONIA PIPING AND INSTRUMENTATION DIAGRAMS (P&IDS):
P&IDs and Specification Development
Divya Engineering provides comprehensive services by developing Piping and Instrumentation Diagrams (P&IDs) for ammonia systems. These diagrams represent the layout and components of the piping system, including valves, pumps, instrumentation, and control systems. P&IDs are essential for simplifying troubleshooting and maintenance while ensuring the safe operation of the system. In addition to P&IDs, Divya Engineering creates detailed piping specifications and standards that define the necessary parameters for installation, operation, and maintenance, ensuring compliance with both local and international safety and reliability standards.

AMMONIA DEVELOPMENT OF PIPING SPECIFICATIONS AND STANDARDS
The development of piping specifications and standards is another cornerstone of Divya Engineering’s turbine piping design services. These specifications ensure that the turbine piping system is designed, installed, and maintained according to consistent, reliable, and efficient practices. This is particularly important in ensuring the safety, performance, and durability of the system, while ensuring compliance with both local and international regulations.
Divya Engineering adopts a structured, phased methodology when developing these specifications and standards, ensuring comprehensive coverage throughout the project lifecycle. This process is essential for turbine piping design, as it guarantees the correct selection of materials, accurate pipe sizing, and adherence to national and international standards. By providing detailed piping specifications, Divya Engineering ensures that turbine systems operate at peak efficiency
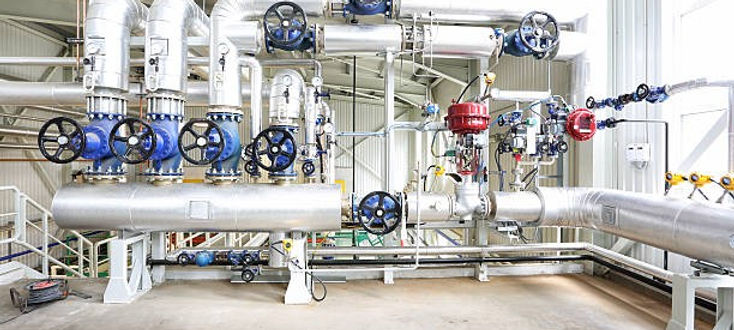
AMMONIA PIPE SIZING AND HYDRAULIC CALCULATIONS
Advanced Modeling and Hydraulic Calculations
To increase the efficiency and cost-effectiveness of ammonia systems, Divya Engineering employs hydraulic calculations and advanced pipe-sizing techniques. These methods ensure that the system operates at peak performance while minimizing operational costs. Through the use of 3D modeling technology,
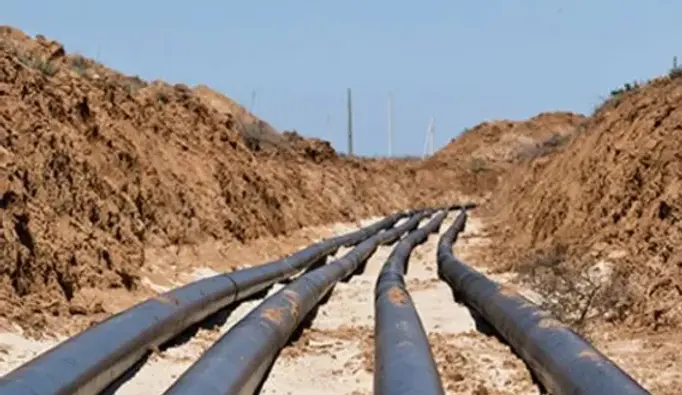
AMMONIA 3D MODELING AND DESIGN
Divya Engineering provides highly accurate visual representations of the ammonia piping system, aiding in better planning, reducing errors, and ensuring more reliable construction outcomes. The 3D modeling approach reduces rework risks and ensures a smoother transition from design to construction.

AMMONIA ISOMETRIC/FABRICATION/ERECTION DRAWINGS
Isometric, Fabrication, and Erection Drawings
Once the design phase is complete, Divya Engineering generates a comprehensive set of Isometric Drawings, Fabrication Drawings, and Erection Drawings. These drawings are crucial for the precise construction and installation of ammonia systems, ensuring that each component is fabricated, assembled, and installed according to specifications. Isometric drawings provide a 3D perspective of the system, while fabrication drawings detail the individual components and materials. Erection drawings guide the on-site assembly process, ensuring that the final installation aligns with the original design.
By offering these full-service capabilities, Divya Engineering guarantees the successful design, implementation, and operation of ammonia piping systems that are safe, reliable, and efficient, even in demanding industrial environments. Their commitment to quality, innovation, and compliance ensures that each fuel transportation system meets the highest standards of safety and performance.
This version replaces the term "Naphtha" with "Ammonia" and provides an expanded overview of Divya Engineering’s services in the context of ammonia piping system
Ammonia Piping Design Services
Piping Design Consultants- Ammonia Piping | Divya Engineering
Piping Design and Drafting: Creating detailed CAD drawings and design calculations for Ammonia piping systems used in power plants, refineries, and other industrial facilities.
​
Pipe Stress Analysis: Performing static and dynamic stress analysis using software like CAESAR II to ensure the Ammonia piping system can withstand operational and environmental stresses.
​
3D Modeling and Design: Using software such as PDS, PDMS, or Auto Plant to create 3D models of Ammonia piping systems for better visualization and accuracy.
​
Isometric/Fabrication/Erection Drawings: Preparing detailed drawings for the fabrication and installation of Ammonia piping systems.
​
Support Detail Drawing Preparation: Designing and detailing the necessary supports for the Ammonia piping system to ensure stability and safety.
​
Project Management: Managing the entire Ammonia piping design project from initial conceptualization through fabrication and commissioning.
​
Compliance with Standards: Ensuring that the design complies with relevant standards such as ASME B31.1 for power piping and ASME B31.3 for process piping.
​
BILL OF MATERIAL, INSULATION & EXPANSION JOINTS
​
​
Challenges Ammonia piping System design
​
Designing Ammonia Piping Systems presents several unique challenges due to the hazardous nature of ammonia, its physical and chemical properties, and the complex operational requirements of ammonia-based systems. Below are the key challenges faced in the design of ammonia piping systems:
1. Material Selection and Corrosion Resistance:
Ammonia is highly corrosive, and exposure to air or water can exacerbate its corrosive effects on many materials. Designers must carefully select materials that are resistant to ammonia’s corrosive properties. Common materials for ammonia systems include carbon steel (with protective coatings), stainless steel, and other specialized alloys. The challenge lies in ensuring the materials can withstand both the chemical aggressiveness of ammonia and the operational conditions, including pressure and temperature fluctuations.
2. Leak Prevention and Detection:
Ammonia is toxic, corrosive, and highly hazardous if leaked into the environment, making leak prevention a top priority. Piping systems must be designed with leak-proof joints, flanges, and seals to minimize the risk of ammonia leaks. Incorporating real-time leak detection systems and continuous monitoring is also essential. The design must also ensure that there are no hidden areas where leaks could occur unnoticed. Additionally, emergency shut-off valves and containment systems should be part of the design to mitigate the effects of leaks.
3. Pressure and Flow Control:
Ammonia is typically transported at high pressures in a liquid state, but it may vaporize when exposed to lower pressures. Maintaining constant pressure and flow within the system is critical to ensuring safe and efficient operation. The piping design must integrate pressure regulators, control valves, and relief valves to manage pressure levels and prevent over-pressurization, which can result in ruptures or leaks. Flow meters and pressure gauges should also be strategically placed to monitor system performance in real-time.
4. Temperature Sensitivity:
Ammonia can have varying properties depending on the temperature, and it can rapidly vaporize at higher temperatures. Designers must account for thermal expansion and contraction in the piping system, especially in environments with fluctuating temperatures. Thermal stress can lead to pipe failure or leaks, so expansion joints and insulation materials must be considered. The system must also ensure that the ammonia remains in its liquid form under normal operating conditions, which could require refrigeration or the use of insulated piping in specific areas.
5. Vibration and Mechanical Stress:
The equipment used in ammonia systems, such as pumps and compressors, can generate vibrations that may lead to mechanical stress on the piping. Over time, this can cause wear on joints, valves, and flanges, potentially leading to leaks or failures. To mitigate these risks, vibration dampening systems, flexible joints, and proper pipe supports must be integrated into the design to reduce mechanical stress and maintain system integrity.
6. Fire and Explosion Risk:
Ammonia is not flammable, but it can pose a significant explosion risk in the presence of an ignition source, especially if mixed with air at the right concentration. While ammonia itself is not as flammable as other chemicals, its ability to form explosive mixtures with air in certain conditions requires that the piping system be designed to avoid such risks. This includes proper grounding of equipment to prevent static discharge, ventilation systems to dissipate any ammonia vapors, and the use of flame arrestors and explosion-proof components in critical areas.
7. Environmental Protection:
Ammonia is a hazardous material with significant environmental impacts in the case of spills or leaks. A leakage into the surrounding environment can lead to severe contamination of soil, water, and air. As such, the design of ammonia piping systems must include containment systems, such as double-walled pipes or secondary containment trenches, to contain potential spills. The system must also comply with environmental regulations, which can vary by region, to ensure that ammonia handling does not pose a risk to the environment.
8. Regulatory Compliance:
Ammonia piping systems are subject to strict industry regulations and safety standards set by organizations such as the Occupational Safety and Health Administration (OSHA), the American Society of Mechanical Engineers (ASME), the American Petroleum Institute (API), and local environmental and safety authorities. Meeting these regulatory requirements can be a complex and time-consuming process, requiring careful documentation, risk assessments, and validation that the design meets or exceeds safety and environmental standards.
9. System Integration:
Ammonia piping systems are often part of a larger facility infrastructure, such as refrigeration systems, chemical plants, or fertilizer production units. Integrating the ammonia piping system with other systems, such as pressure vessels, heat exchangers, or storage tanks, presents several design challenges. It is crucial to ensure that the ammonia system operates seamlessly with other facility systems while preventing conflicts between piping routes and other infrastructure.
10. Maintenance and Inspection:
Ammonia piping systems require ongoing maintenance to ensure safe and reliable operation. The design must allow easy access to critical components such as valves, pumps, and pressure relief devices for regular inspection and maintenance. The system should be designed to minimize downtime during maintenance and provide adequate space for personnel to safely carry out repairs or replacements. Regular inspection of joints, flanges, and seals is essential to prevent unnoticed leaks or degradation.
11. Cost Management:
Designing ammonia piping systems involves the use of specialized materials and components that are resistant to ammonia's corrosive properties. These materials, along with the need for advanced safety features and regulatory compliance, can drive up the cost of the project. Balancing cost considerations with safety, durability, and system performance is a challenge for designers, particularly for projects with budget constraints. It’s important to select cost-effective materials and design features without compromising safety or compliance.
12. Aging Infrastructure:
In many cases, ammonia piping systems are part of older infrastructure, which may have been designed with outdated standards or materials. Upgrading or retrofitting these systems can present challenges, including the need to meet modern safety and regulatory standards while ensuring compatibility with the existing infrastructure. Addressing wear and tear, corrosion, and system inefficiencies in older systems is often required during retrofits.
Addressing these challenges requires a high level of expertise in chemical handling, material science, system design, and safety protocols. Successful ammonia piping system design ensures safe and efficient transport while protecting both people and the environment, all while complying with regulatory requirements and optimizing cost-efficiency.
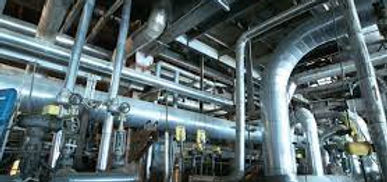

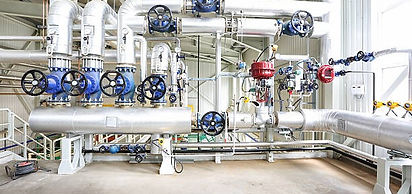
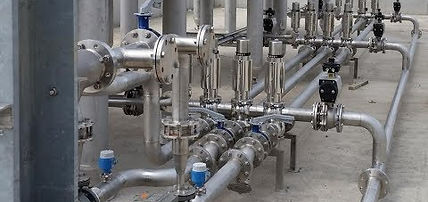